Henrik Sollie joined the Norway-based company Pipeotech in late 2018, though the first pilot installation of the company’s patented technology began as early as 2012.
“The inventor’s true motivation was to remove the weakest link in industrial piping and to create a gasket that ensures that the joints are as strong as the pipes themselves. The difficulties associated with existing sealing technologies motivated him to take up the challenge of developing a new technology that would change the perception of a gasket from being a consumable after-thought to an integral durable product.”
Some of Pipeotech’s primary goals were to develop a gasket that would last significantly longer, exceed a gas-tight strength, and eliminate the need for maintenance. Metal-to-metal sealing technology was a technique that had previously been reserved for subsea oil and gas applications where meeting the most extreme operational criteria is required. Adapted directly from the same sub-sea technology, they designed a single metal gasket for raised faced and flat faced flanges.
With a goal of providing exceptional gasket products to the industrial market, supported by strong quantitative data, the company spent half a decade testing their technology to back-up the unique claims of the DeltaV-Seal.
Pipeotech set out to make a difference with their game-changing concept. “We challenge our clients to move away from specifying a brand or generic design and instead define what performance they want from the gasket. We want them to ask themselves; What do you consider an acceptable leak rate? Should the gasket dictate your maintenance schedule and your shut down intervals? Is increased frequency of leak detection and repair (LDAR) the way to abate fugitive emissions, or will it be better to replace leaking components with leak-proof components?”
As CEO, Sollie manages overall operations for the company and mentions that the biggest challenge they face in the industrial sealing space is to change the perception of what a gasket really is. “A gasket is considered, and I quote; a mechanical device that enables low-leakage service. It’s broadly accepted that gaskets leak harmful toxins from start-up and that they degenerate quickly, with leakage increasing during their short service life. Building a new company coming from the outpost of Norway and telling entire global industries that they can do things much smarter is a challenge, but the potential to truly make an impact gives us energy to persevere.”
“Another obstacle to overcome is choosing the correct gasket early in system design process. Sealability, chemical compatibility, and blowout resistance will be compromised when gaskets are not given proper consideration at the correct stage in the design process. The common data used for evaluation, like M&Y factors, temperature limits, chemical- and creep resistance is not sufficient in a start-up, stay-up driven focused project. Neither will it meet the coming requirements for mitigating fugitive emissions.”
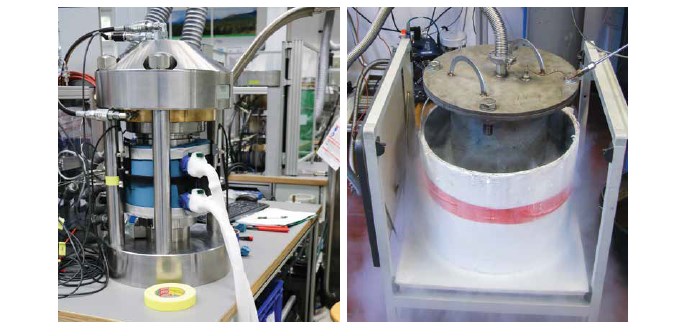
With a full gamut of sealing options available, Pipeotech offers a unique position that urges end users to swap out old-fashioned gaskets for full metal DeltaV-Seals, which ensure the joints in a piping system are as strong as the pipes themselves. The patented, revolutionary technology is a one-piece, CNC manufactured gasket made from material compatible with the flange it mates with. Three sharp, unique sealing rings deform on installation, filling any irregularities on pipe flanges to form a complete seal. Once placed between the connecting flanges, a permanent, static and leak-proof seal is created. “Our core focus is on the small details of the design, the materials, and the manufacturing process. There are benefits to product simplicity, but only if you know how to translate every detail into something an end user can understand and see the value of using,” said Sollie.
With the incumbent technology widely in use today, the inevitable deterioration of filler materials, galvanic corrosion, and loss of tightness from temperature fluctuations all contribute to preventable leakages. Expensive maintenance schedules are required to constantly re-torque and replace failing gasket technology in an effort to overcome what should be considered a fundamental design flaw. DeltaV-Seal performs better, and the company can prove it. “We have eliminated the weakest link in a piping system. When you bolt up the connection or the joint, there will be a seamless interaction,” he continued.
In demanding environments, such as hydrocarbon services or seawater, gasketed flanges are subject to aggressive forces of corrosion and deterioration. With the DeltaV-Seal, the flange compatible material used in manufacturing mitigates the risk of galvanic corrosion in the connection.
Testing & Performance
Since its initial development in 2012, the DeltaV-Seal has undergone an extensive test program (see sidebar box). Rigorous laboratory and real-world tests are conducted with recognized and respected industry authorities such as Amtec and DNVGL. To date, the DeltaV-Seal is the only recipient of type approval from DNVGL, due to a combination of its outstanding leakage and longevity performance. Throughout other standardized testing procedures such as EN-13555 and Shell MESC SPE 35/300, the DeltaV-Seal also exhibited exceptional results.
A perfect example would be a recent test conducted by the University of Wrocław in Poland. It was established that for cryogenic applications (LNG shipping, terminals, regasification etc.) where operating temperatures are often approaching -196°C, the DeltaV-Seal maintains a tightness higher than 10-8 mg/s (3.6*10-11 kg/h) at all tested pressures. When compared to other gaskets that have undergone similar testing at lower pressures (spiral-wound + graphite, Kammprofile + graphite & Kammprofile + PTFE) comparisons show that the DeltaV-Seal was more than 10,000 times tighter. While the other technology stopped testing at 8 bar – we continued to 100 bar and maintained a perfect gas-tight seal.
Based on these tests we calculated that for cryogenic ap-plications, each flange containing a DeltaV-Seal would save at least 1.1*10-4 * 24 * 365 ≈ 1 kg/year of Methane + NMVOC emissions.
With extensive tests verifying not only the exception-al sealing qualities of DeltaV-Seal, but also how it performed over time, the idea was born to back up these extreme results with a zero-leakage warranty. “The simple yet unique properties of the gasket allowed for unique claims. Back in 2019 we decided to back up these claims with the industry’s first and only 10-year gas-tight limited warranty. We believe the value proposition of a sealing product that offers a guaranteed level of tightness over such a long time represents a generational leap for the sealing industry. For us it was essential that the warranty became applicable for as broad a range of applications and processes as possible, so we continue to push the boundaries with testing to broaden our offering.”
Pipeotech accommodates new and more stringent regulations for governments and standardization bodies. “The gasket industry claims to meet today’s stringent regulations. The fact is that requirement of today is far from stringent to be honest. The first time a maximum permissible leakage rate was added to the ASME B16.20 standard ‘Metallic Gaskets for Pipe Flanges’ was in 2017! We are now leading an initiative with the relevant international regulatory bodies to make sure that gasket leakage performance and regulation is more closely aligned with the ambitions and targets of the Paris Agreement.”
“We can guarantee there will be no need for retorque for at least 10 years in any application. As the gasket will not leak, and the frequency in which leak detection and repair (LDAR) programs are used would be greatly reduced, saving companies downtime, product, and revenue. We like to say, ‘Why leak and repair when you can install and forget’.”
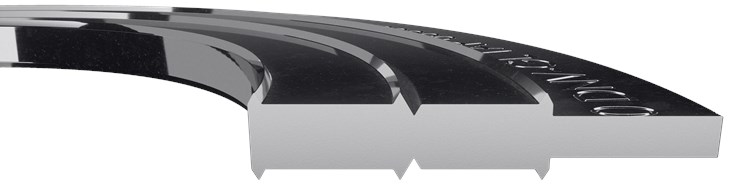
The company understands that good business goes hand in hand with environmental stewardship. By manufacturing a gasket seal that completely eliminates fugitive emissions, with zero leaks, no product loss, and maximum efficiency, the manufacturer is helping other companies safeguard not only their reputation, people, and assets, but the environment in a largely impactful way.
“The DeltaV-Seal technology has the tightest sealing properties and lowest leakage rates available for pipe-line connections today,” said Sollie. “We will continue to work with associations like the European Sealing Association (ESA), and Assosiation for Material Protection and Performance (AMPP) to develop standards for a sustain-able future. The more critical the application, the higher the pressure, temperature or abrasiveness of the media, the more challenging the environment and as an industry we must always be prepared.”
Pipeotech aims to deliver absolute pipeline integrity for its customers and transform standards for industrial piping, one seal at a time.
Summary of Significant DeltaV-Seal Certifications & Tests
Shell MESC 85/300
The Shell Specification MESC SPE 85/300 describes several testing procedures for the evaluation of the gasket’s compressibility and the tightness characteristics of the gasket material at ambient and elevated temperature.
• Shell leakage test at ambient temperature (MESC SPE 85/300 – 3.3.2)
• Shell leakage test at 400oC (MESC SPE 85/300 – 3.3.2)
• Compression test at ambient temperature (MESC SPE 85/300 – 3.3.4: EN 13555)
• Compression test at 400oC (MESC SPE 85/300 – 3.3.4: EN 13555)
• Relaxation test at ambient temperature (MESC SPE 85/300 – 3.3.4: EN 13555)
• Relaxation test at 400oC MESC SPE 85/300 – 3.3.4: EN 13555)
• Leakage test (MESC SPE 85/300 – 3.3.4: EN 13555)
• HOTT Shell cycle test at 400oC (MESC SPE 85/300 – 3.3.5)
• Hot Blowout Test at 400oC (MESC SPE 85/300 – 3.3.6)
Fire Safe Test – API 6FB
Fire test approved, high temperature (650°C), AMTEC cert. no. 30328901E/CS/28.10.16
Tightness Test – VDI 2440
TA-Luft helium test approved for low emissions, AMTEC cert. no. 30328902E/BU/28.10.16
DeltaV-Seal can be characterized as “A high-grade sealing system for the purposes of TA-Luft”
DNV GL Type Approval
The world’s first DNV GL type approved flange sealing, approved for use with ASME B16.5 and EN 1092-1 flanges. Tests in the series included…
• Vibration testing
• Leakage tests
• Burst pressure tests
• Pressure pulse tests
Cryogenic Test
Leakage test of a pressurised bolted flange joint dipped in liquid nitrogen conducted with the university of Wroclaw, Poland.
The test results show that DeltaV-Seal™ has an extreme level of tightness at cryogenic temperatures down to -196°C at pressures from 10 bar to 100 bar. Based on these tests, it was found that DeltaV-Seal maintains a tightness higher than 10-8 mg/s.
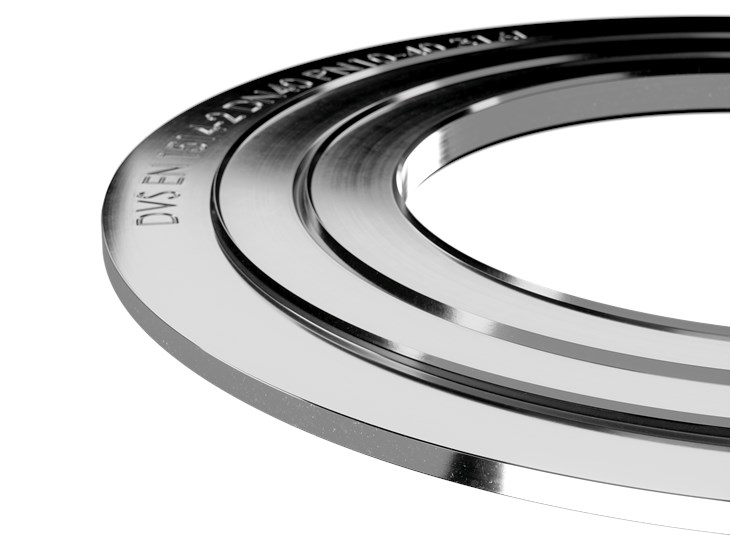