Alfred Kruijer, Principal Technical Expert for Piping & Valves at Shell, introduces a new testing method for fugitive emissions using forming gas, in collaboration with Emiel Lechevallier from Ventil Test Equipment. This approach aims to improve industry practices by enhancing safety, reducing environmental impact and lowering costs for valve manufacturers and energy companies. It offers the potential to contribute to better standards across the sector.
By KCI Editorial
In an industry where innovation is important but often approached cautiously, Alfred Kruijer has been a steady advocate for progress. With nearly four decades of experience at Shell, Kruijer has consistently championed environmental responsibility and ethical practices in emissions testing and valve performance standards. His latest collaboration – with Ventil Test Equipment – has contributed to the development of a new testing methodology for fugitive emissions, aimed at addressing longstanding cost and safety concerns.
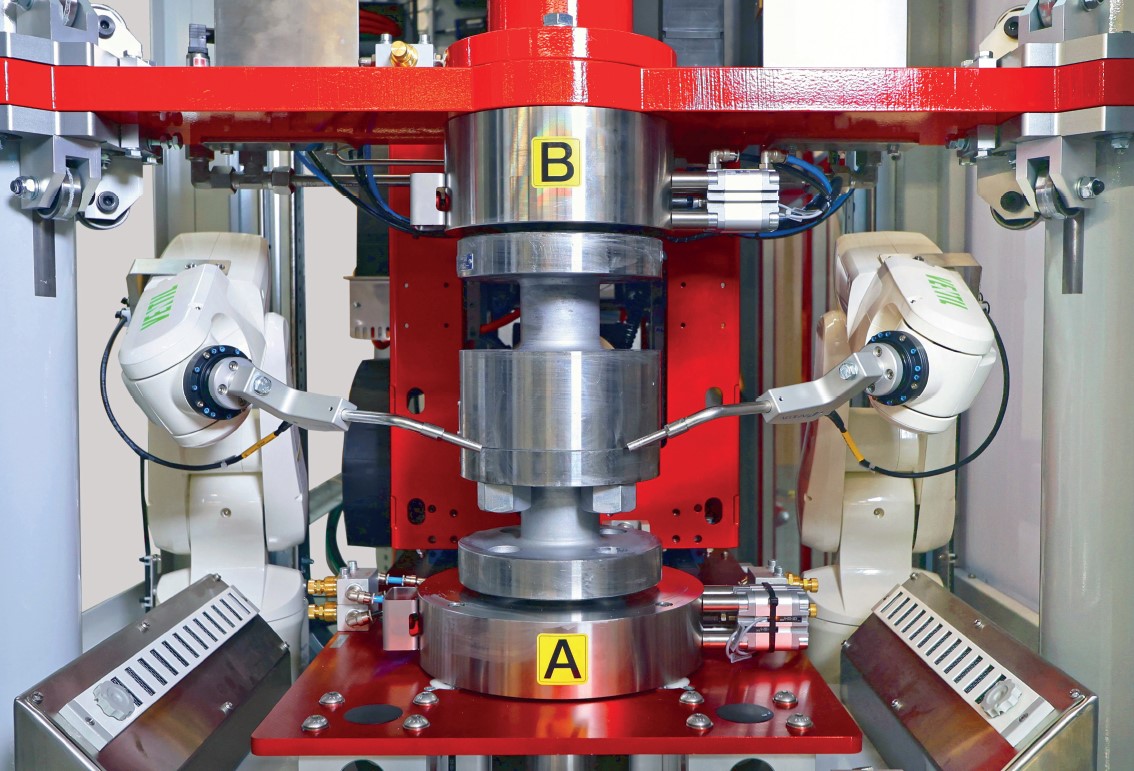
A career shaped by adaptation and progress
Kruijer’s journey at Shell had an unassuming beginning in 1985. “When I started almost 40 years ago, assignments were simply given to you,” he recalls. “You went where the company needed you, and that was just the norm.” This modest start, however, laid the foundation for a career characterized by continuous learning and adaptation. Kruijer’s willingness to embrace new challenges and opportunities has been crucial in an industry that must remain responsive to society’s evolving needs.
Throughout his tenure, Kruijer has witnessed and contributed to significant changes in the industry’s approach to environmental and safety concerns. “Consciousness of environmental concerns has been growing since before I joined Shell,” he notes. As his career progressed, Kruijer’s focus shifted from merely following assigned roles to actively shaping industry standards and practices. His commitment to responsible practices became central to his work as he realized the substantial impact of individual actions and corporate policies on safety, environment and society.
Championing fugitive emissions testing emerged as a critical focus area for Kruijer. He understood its importance in reducing the industry’s environmental footprint. “Shell has a long history of advocating for improved standards in fugitive emissions testing,” Kruijer explains. “Early on, we connected with other European-based international oil and gas companies, recognizing the importance of a collective effort to drive change in the industry.”
Kruijer’s advocacy for stringent fugitive emissions performance standards was often met with caution and scepticism. The oil and gas industry, known for its conservative approach to adopting new technologies, due to safety concerns, presented a challenging environment for innovation.
However, Kruijer’s persistence, coupled with thorough research and collaboration with experts, led to a deep understanding of the science and of the technological improvements that could enhance testing methods and performance standards. “Shell is a company that values transparency and collaboration, with a commitment to ethical decision making,” Kruijer states. This approach has been instrumental in advocating for higher standards and more sustainable practices across the industry.
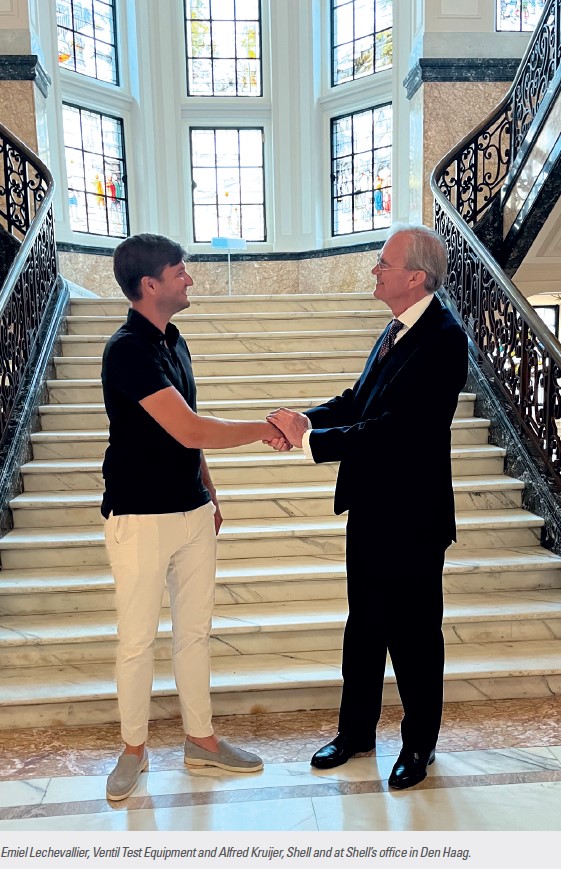
A chance encounter leads to breakthrough
The story of forming gas as a leak testing alternative began with a chance encounter at a Valve World Conference. It was Emiel Lechevallier from Ventil Test Equipment who introduced Kruijer to the concept of using forming gas instead of helium for leak testing. This serendipitous meeting would lead to a collaboration that would challenge industry norms and potentially revolutionize leak testing practices.
Kruijer explains, “This concept caught my attention because safely conducting fugitive emission testing at our required levels has been a significant challenge.” The innovation addresses two longstanding industry concerns: the escalating costs of helium-based testing, and the safety and environmental risks associated with methane use indoors as an alternative, much debated because LDAR programs are historically benchmarked on methane.
Validating the forming gas approach
Kruijer and Lechevallier conducted an extensive series of experiments across various scenarios to evaluate forming gas performance, reliability and theoretical foundations. Their goal was not just to prove the effectiveness of forming gas but to create a comprehensive body of evidence that could withstand scrutiny from industry peers and regulators.
“We started by examining the theoretical basis,” Lechevallier explains. “We distilled our findings into a few key formulas that describe gas behaviour during fugitive emission tests. This process raised an important question: What is the size of a typical fugitive emission and how does it behave under different conditions?” Their research yielded surprising insights, challenging common assumptions about gas behaviour. Lechevallier reveals, “We discovered that helium excels at detecting very small leaks – what we call fugitive emissions. Interestingly, for larger leaks, methane escapes much more rapidly than helium.” This counterintuitive finding highlights the critical importance of thorough research in driving innovation within the field.
The validation process was both rigorous and comprehensive, combining laboratory tests with field trials. Lechevallier explains, “We established a lab with calibrated leaks to generate reproducible reference values.” This approach enabled them to determine a reliable conversion factor between helium and forming gas measurements, aligning with accepted emission classes in existing industry standards.
Kruijer and Lechevallier’s dedication resulted in a published paper in the ASME PVT journal that presented their discoveries. This publication has opened the door for forming gas to be widely considered as a safe, economical solution for fugitive emission testing.
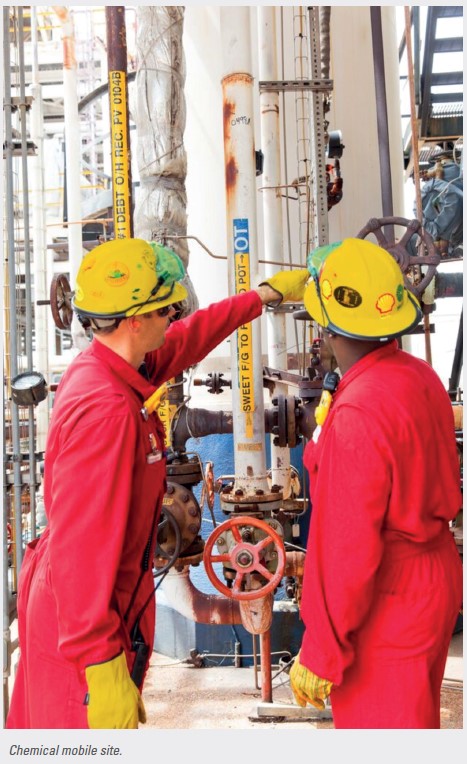
The compelling case for forming gas
Despite the industry’s seeming sluggishness in adaptation, Kruijer firmly believes the benefits of adopting forming gas as an alternative to helium are too valuable to overlook. The advantages of this switch are multifaceted and compelling:
- Cost-effectiveness: Forming gas offers significant savings compared to the increasingly scarce and expensive helium. Lechevallier explains, “the switch to forming gas testing equipment quickly pays for itself. Based on current prices, the cost savings from just four bottles of helium cover the investment in new forming gas equipment. This rapid return on investment makes it an easy decision for most companies.”
- Safety: Forming gas is a safe alternative compared to testing with methane, so it addresses a critical safety issue by minimising technicians’ exposure to hazardous gases during testing. This aligns perfectly with the industry’s paramount concern for worker safety.
- Operational efficiency: User friendly leak detection equipment makes handling and test procedures much simpler, which directly leads to efficiency and clarity in test results. The ease of use will facilitate more rapid adoption, enhancing overall safety and compliance.
- Sustainability: Saving finite resources like helium for important developments like deep cryogenics, medicine and science. This aligns with the industry’s growing focus on sustainability: maintaining safe, high-quality practices without depleting critical resources.
- Consistency in testing: “Forming gas provides more stable test results throughout the day,” Lechevallier explains. “It disperses quickly, so even if you open a door, the gas does not linger or build up in the room. This means you can perform consistent tests all day long. In contrast, when using helium, its tendency to accumulate in the room can skew test results as the day progresses.”
- Versatility: The potential applications of forming gas extend beyond fugitive emissions testing. “We’ve been getting questions about using forming gas for other applications,” Lechevallier notes. “If you have a seat leakage and want to find out where it is coming from, or if you want detect pinhole leakages in castings, the gas is cheap enough to run extensive tests. It opens up a whole new range of possibilities for valve diagnostics.”
Breaking through resistance
While the benefits of forming gas are clear, Kruijer acknowledges the challenges in achieving widespread adoption in the oil and gas industry. “We do not seem to pivot quickly enough,” he notes. This reluctance to change stems from an understandable preoccupation with risk mitigation in an industry where safety is paramount. However, Kruijer’s approach to driving change is methodical and persistent. Rather than trying to circumvent established practices, he leverages his hard-earned credibility to open dialogues with key decision-makers. By presenting comprehensive data that validate forming gas’s efficacy and safety, he aims to gradually shift mindsets and demonstrate that responsible innovation is vital for long-term sustainability.
A path to industry wide adoption
Kruijer and Lechevallier’s efforts to promote forming gas have already gained traction within the industry. Their work has been incorporated into API 6Z (now Annex M of API 6D), which focuses on hydrogen gas valves. This inclusion marks a significant step towards broader acceptance and standardization. The next goal is to incorporate forming gas testing into ISO 15848, the international standard for fugitive emissions testing. With the standard approaching its revision cycle, there’s a window of opportunity to influence industry practices on a global scale.
“The adoption of forming gas testing is a valuable opportunity for the industry,” Kruijer states. “Rather than overlook or dismiss it, consider how it could offer benefits. Shell represents only a small fraction of the oil & gas sector, so broader adoption is essential for meaningful impact.”
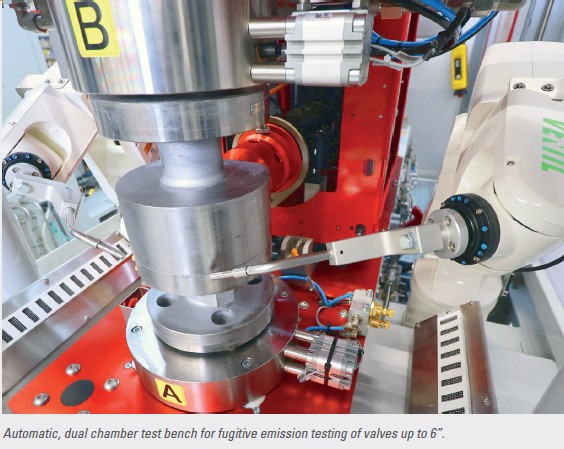
A future of sustainable innovation
The introduction of forming gas as an alternative for fugitive emission testing arrives at an opportune time, as the industry grapples with helium shortages and rising costs. Kruijer sees this innovation as a catalyst for broader change, potentially sparking an industry-wide embrace of sustainable practices. Beyond fugitive emissions, Kruijer envisions a shift towards green valves. “Fugitive emission performance testing is no longer just about immediate air quality concerns,” he explains. “That’s largely technically solved.”
He continues, “the next frontier is the ‘green valve’. It takes a comprehensive approach to valve design and maintenance. This focuses on reliability and durability to minimize overall emissions throughout the valve’s lifecycle.” Kruijer elaborates, “We consider not just the carbon footprint of manufacturing a valve, but its overall contribution to Green House Gas emissions. This includes factors like repeated replacements, failure to isolate, sluggish control and unreliable actuators.” He concludes, “This approach aligns perfectly with the industry’s increasing focus on long-term environmental responsibility.”
Kruijer’s message to the industry is clear: embrace change, question long-standing practices, and keep pushing forward. For those willing to adapt, the rewards are transformative – optimizing safety, efficiency and ecological responsibility.
Sharing knowledge and driving change
Alfred Kruijer and Emiel Lechevallier, recognized for their groundbreaking work, are taking center stage at Valve World Conference 2024 in Düsseldorf this December. Kruijer will deliver a keynote address, sharing his vision for the future of sustainable valve solutions. The conference will also feature two presentations by Lechevallier:
- On December 4, he will conduct a live demonstration comparing forming gas and helium, offering attendees a practical look at this innovative method in action.
- On December 5, Lechevallier will present the methodology and theoretical basis of their work on forming gas, explaining how it has been incorporated into the first standards.
As the valve industry and energy sector evolve, innovations like forming gas leak testing demonstrate how focusing on environmental responsibility can guide advancements that enhance safety, increase efficiency and reduce environmental impact and cost.
Kruijer’s career-long commitment to improvement and innovation serves as an inspiration to the next generation of engineers and industry leaders. His work with forming gas is not just about a new testing method; it is about creating a culture of continuous improvement and responsible innovation in an industry that plays a crucial role in the global energy landscape. Reflecting on his career and looking ahead, Kruijer’s optimism is evident. “Global warming presents society with immense challenges, but at the same time our ability to solve problems has never been greater. The pace of progress in our field has at no time been more rapid. With global collaboration and instant access to cutting-edge research, we’re solving complex problems faster than ever before. It is an exciting time to be in this industry – the potential for meaningful advancements seems limitless.”
The collaboration between Shell and Ventil on forming gas testing highlights the power of cross-company partnerships in addressing industry challenges. Kruijer and Lechevallier’s work demonstrates that major breakthroughs often result from embracing new ideas and crossing traditional boundaries. Their success proves that technological advancement and environmental protection can be mutually reinforcing goals. As the valve industry evolves, leadership will come from those who embrace innovation, prioritize safety and sustainability, and build strategic alliances – even in unexpected places.
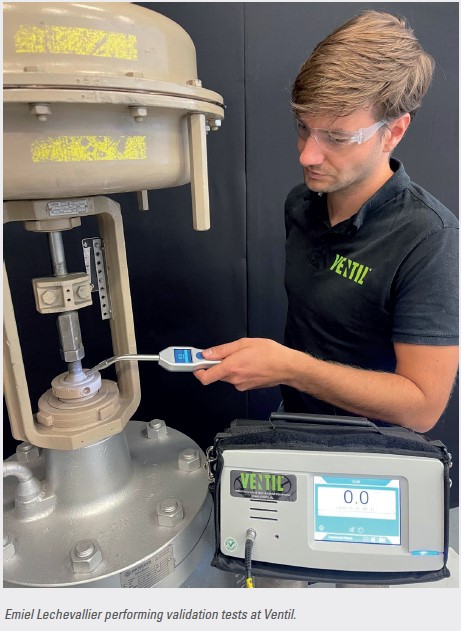