Achieving Class AH tightness for ISO 15848-1 is no easy feat. It demands the fortitude to create innovative designs, perform repeated in-house, customer, and third-party testing, and make changes when improvements are needed. Finding solutions that can meet this level of sealing involves thoroughly understanding the customer’s design criteria, proper material selection, and ensuring the product is designed for a repeatable manufacturing process. Adhering to ISO specifications is a complex challenge for any company, which is why many companies choose to eschew the rigorous steps involved in achieving certification. CDI took the challenge head-on and set its sights on providing its customer with a Class A polymer stem seal that choked off emissions. Remarkably, CDI succeeded.
Fugitive Emissions Journal had the pleasure of speaking with members of the CDI Products team. Mike Hedger, Director of Engineering, Kari Schoeffler, Global Director of Marketing, and Kyle Ward, Product Engineer, provided valuable insights into the company’s path to ISO 15848-1 Class AH/CC1 qualification testing and CDI’s fearless embrace of challenges.
By Kristen Charles, Editor – Fugitive Emissions Journal
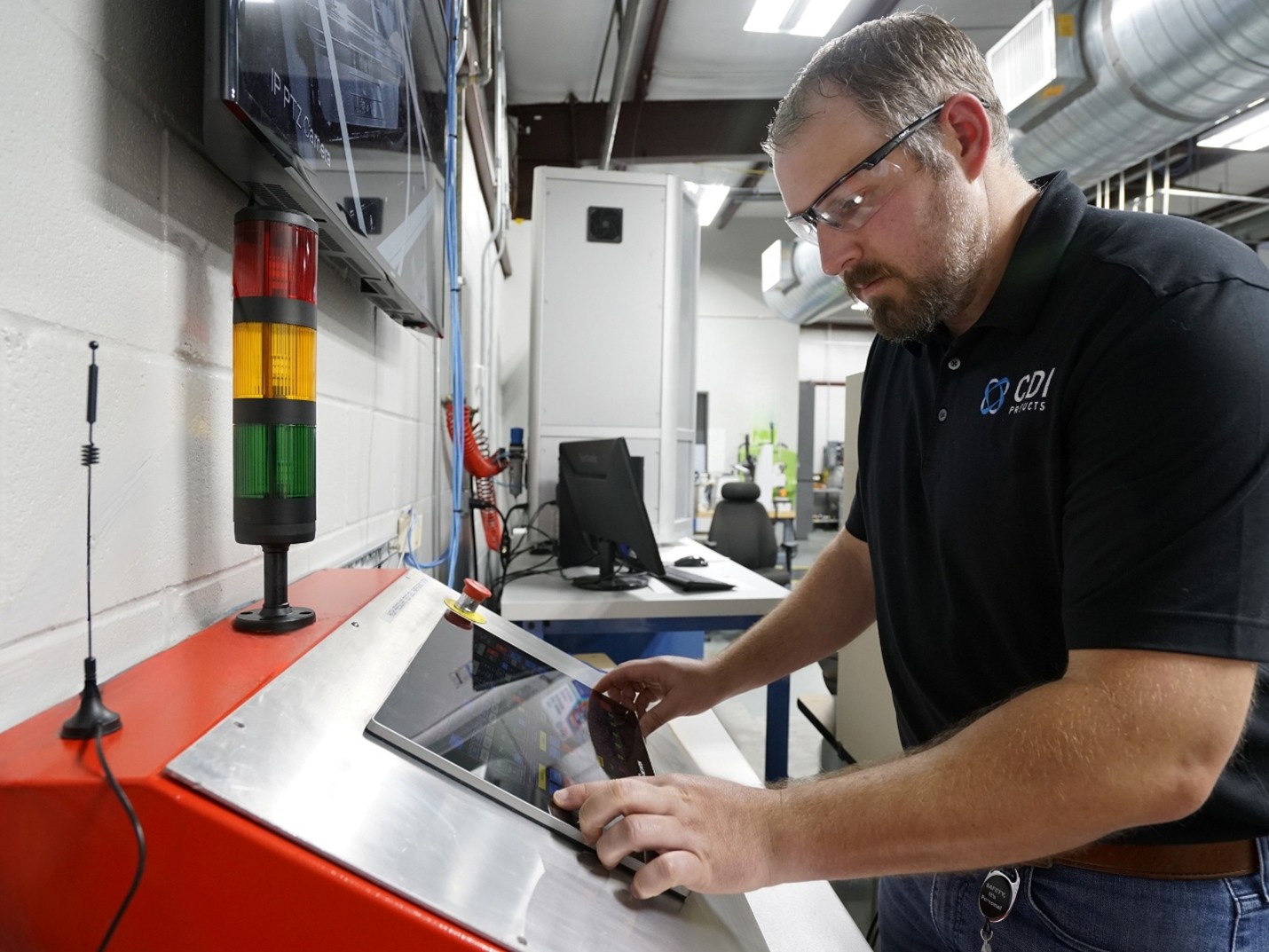
CDI Products is a sealing solutions provider that produces high-performance polymers and flexible graphite products across multiple industries and applications, including oil & gas, energy, aerospace, semiconductors, refineries, petrochemical plants, and medical applications. “In essence, our sealing products protect the OEMs whose equipment we support, the environments that equipment operates within, and the employees and communities who work in and around that equipment each day,” said Schoeffler.
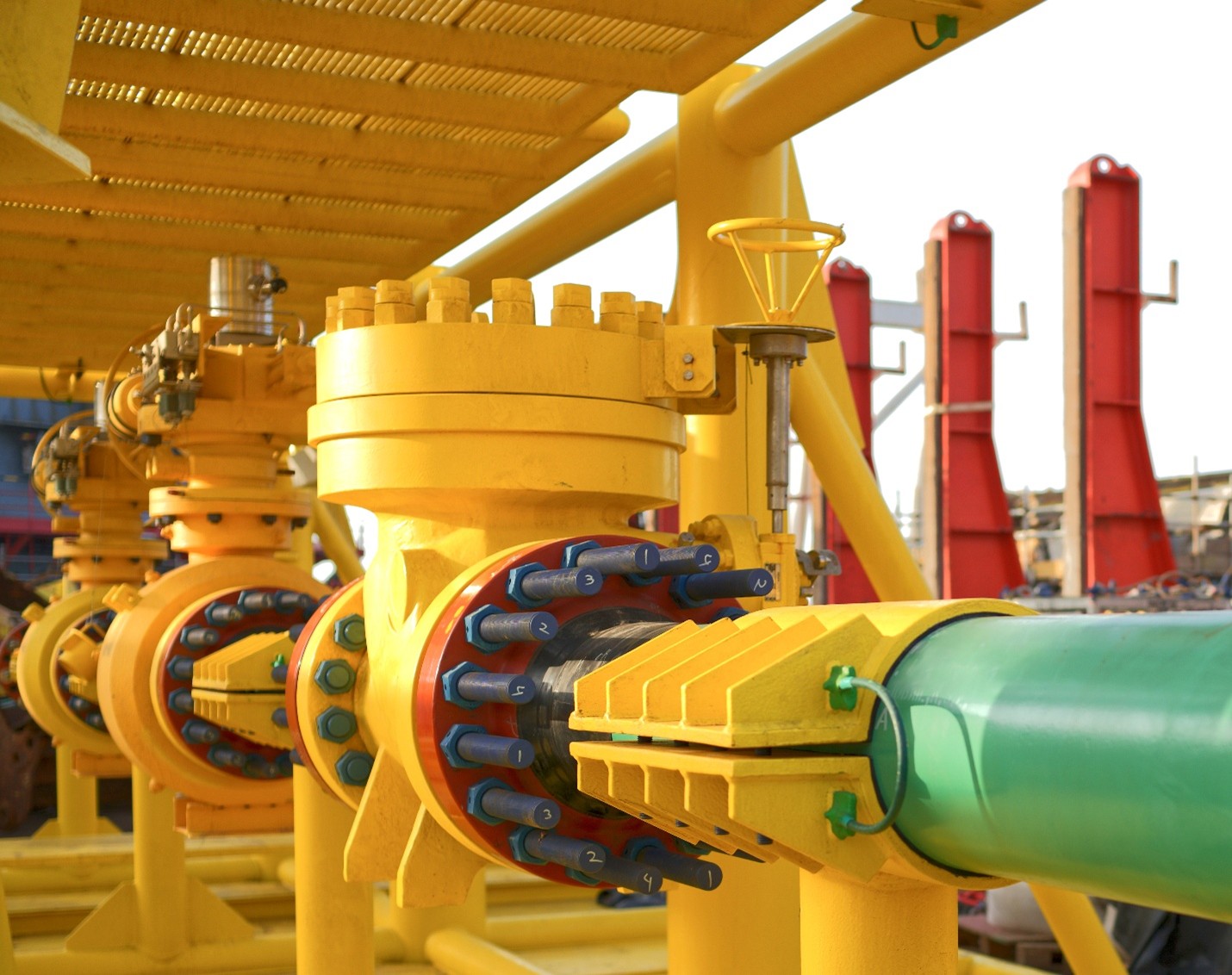
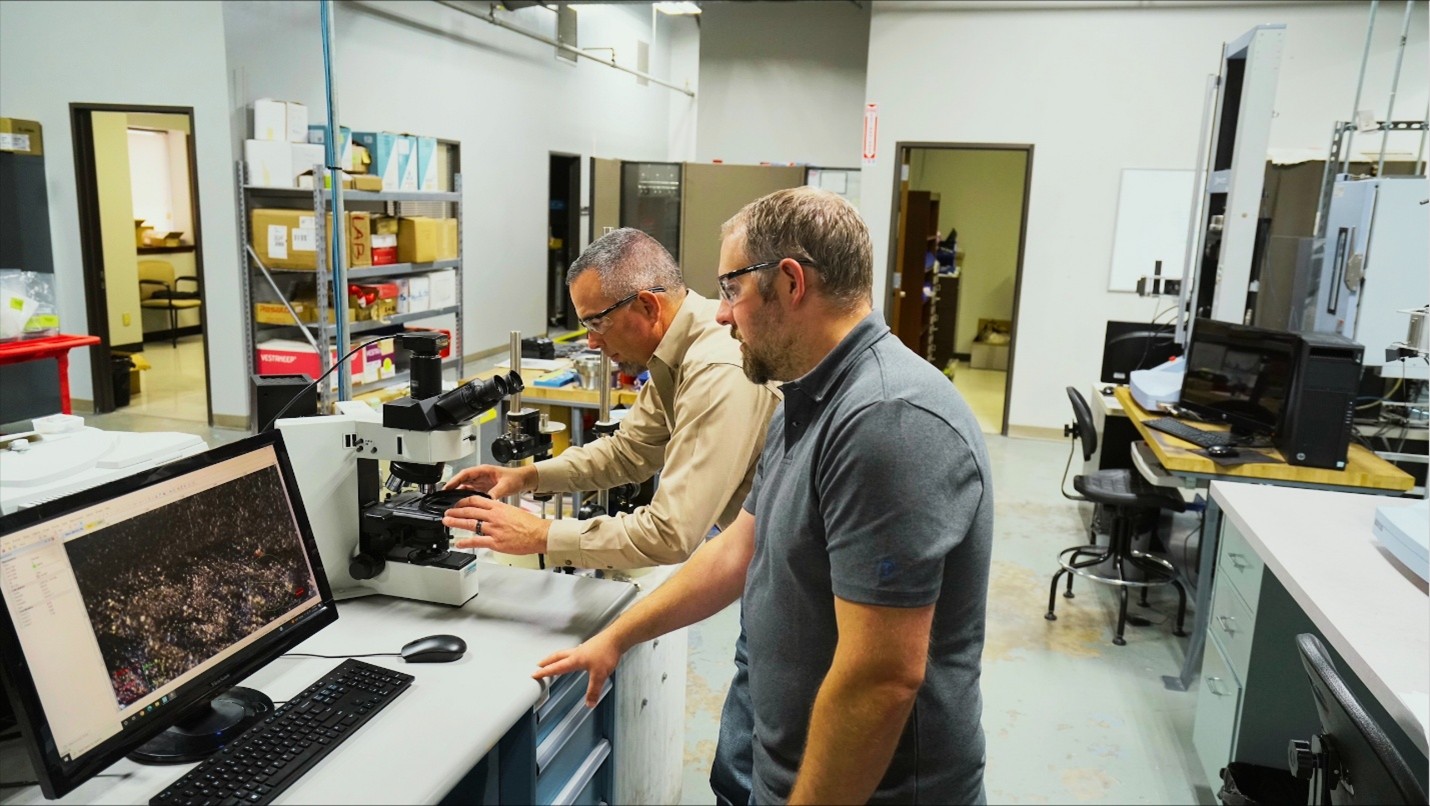
While many sealing companies offer standard products, CDI directs its expertise towards materials and product design, application knowledge, and collaborating with its customers on applications that are challenging yet groundbreaking. “We focus on demanding applications in emerging markets like hydrogen, LNG, and alternative fuels. This is where we are different. We want to tackle the challenge of pushing new technologies past what is expected,” said Hedger. CDI’s material science technologists and engineers collaborate with its customers to pursue evolutionary ventures and develop innovative products with precise specifications.
Ward works with valves and aerospace applications while other members of the CDI team are specialists in other areas, but the entire team understands the dynamics of the different applications. Collaborating with customers in corresponding markets allows CDI to deliver what customers need and meet specifications wherever they are. So, timelines can vary wildly. “Our agility as an organization is driven by our customers’ needs and expectations. That’s at the heart of strong our customer partnerships,” explained Schoeffler.
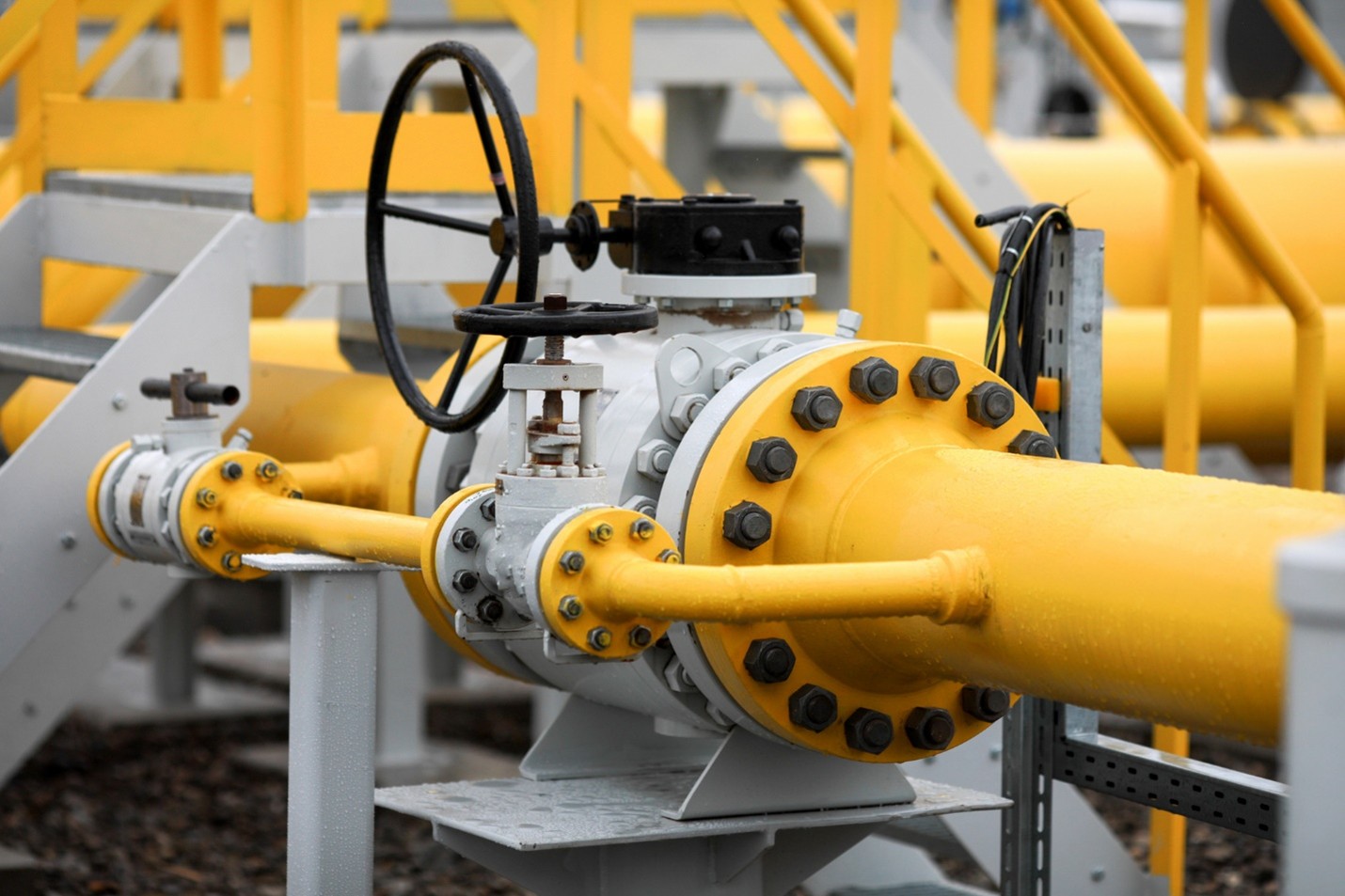
Attaining ISO Qualification
Achieving a level of tightness of Class AH using helium is an immense achievement for CDI. ISO 15848-1 is the standard for testing valve stem seal leakage through a series of mechanical and thermal cycles. The purpose of this standard is to evaluate the degree to which a valve can seal gas, preventing it from escaping into the atmosphere. Helium is a safe gas that is typically used as the test medium to mimic methane without the inherent risks involved with using a combustible gas. However, helium poses its own challenge, as the extremely small helium atoms are far more difficult to seal than the larger methane molecules. The gas also permeates through materials, adding to the sealing difficulty. Couple this with the linear motion the seals see when the valve is opened and closed, and achieving Class AH tightness becomes seemingly impossible. “There is a dynamic interaction between the seals and the stem, which led to CDI having the proper design criteria, geometry, and materials to ensure that the helium does not pass by the seal assembly during the dynamic cycles. It surpasses anything we have done so far,” explained Ward. “Previously, Class AH had been only achieved using metal bellows where the only measured leakage is through the metal itself. Having polymer seals achieve this tightness class means our customers can use simpler, more traditional valves in applications requiring fugitive emissions certification.”
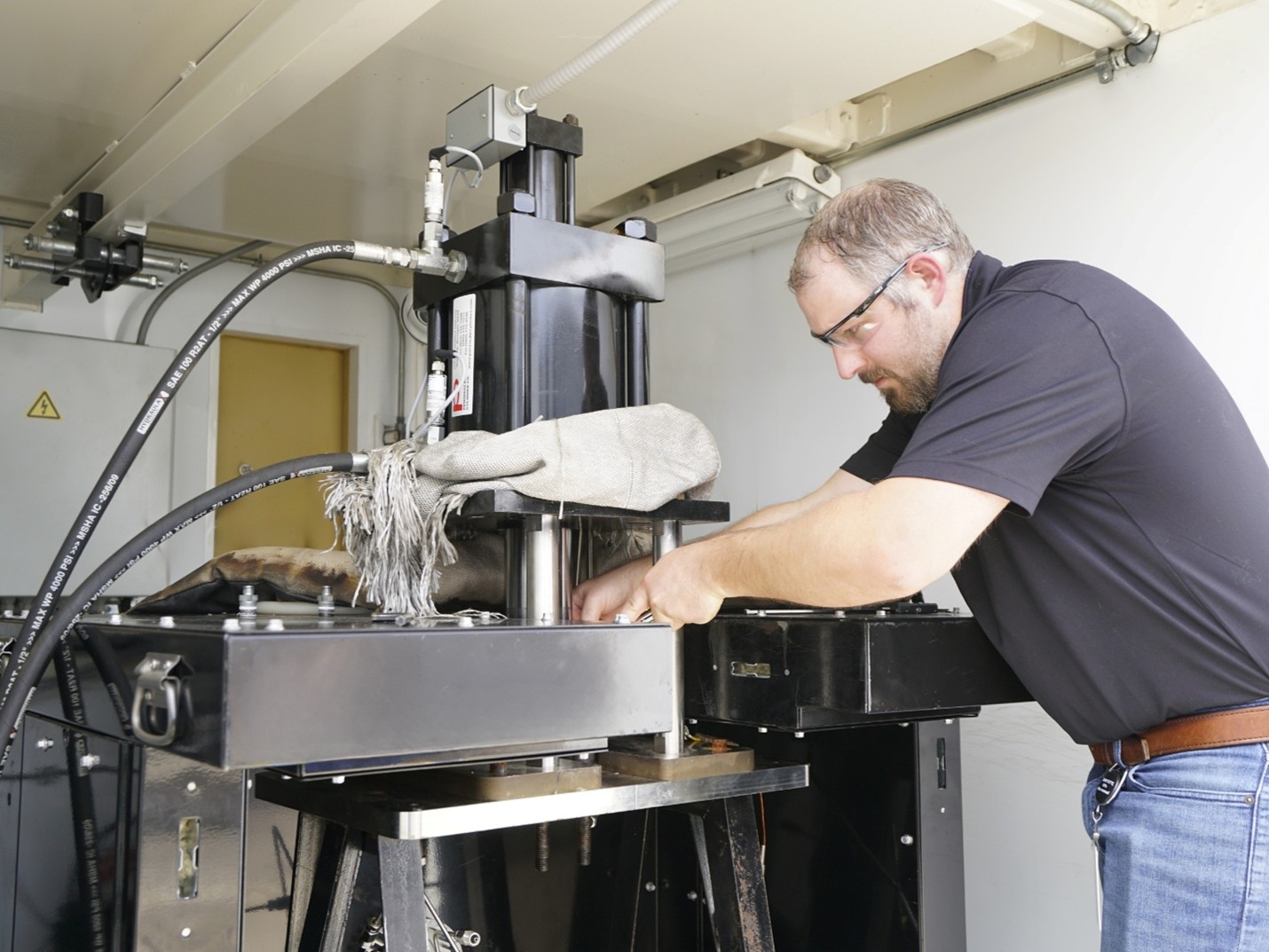
Measuring Cycles
During the ISO 15848-1 test, the valve is opened and closed many times to approximate actual performance in the field. The endurance class sets the requirement for the number of mechanical cycles the valve must endure while leakage is measured. CDI’s seal tested at CC1, which equates to 20,000 mechanical cycles at pressure, with 10,000 cycles at high temperature and 10,000 cycles at low temperature. Leakage detection occurs continuously throughout the test, so it is crucial that CDI’s seals maintain their integrity throughout the 20,000 cycles, not just at ambient temperatures but during the extreme temperatures as well. “We stepped up our cycle count and lowered our leakage rate. We made it to the next tier of our product line offering, and that is why this is so monumental for us,” enthused Ward.
Executing the Process
The CDI process typically begins with a customer’s request for a solution. “We work collaboratively with our customers to ensure we fully understand all of their application details before we begin working,” said Ward. CDI then uses that information to design seals, bearings, functional components or other elastomer, thermoplastic, or other polymer-based material product that will meet their customer’s requirements. Using their in-house knowledge of seal design and simulation tools like Finite Element Analysis (FEA), CDI determines the best seal geometries, component configurations, and materials that best meet the application and testing requirements. CDI’s manufacturing team becomes involved at this stage, working in design for manufacturability mode, or DFM, to ensure design elements are repeatable and manufacturable. “At this point in the project, we validate that the product we are offering is manufacturable, repeatable, and delivers on all our criteria success points,” explained Ward. “Our in-house engineers and material scientists ensure we are offering the correct material for the application. We enlist our design experience from previous successful sealing applications to make sure the whole system works together.” The team at CDI creates drawings which the company then shares with its customers to convey how they intend to solve the application.
Collective Testing
Testing can often be performed by multiple parties to ensure CDI’s seals will meet their requirements. CDI can perform in-house testing before shipping the product to the customer to simulate how the seals perform in a test fixture that approximates the customer’s equipment. The customer typically tests CDI’s seals in its equipment to industry specifications which are driven by the end user. Additionally, often a third-party can be contracted to perform testing when the customer is unable to perform the test themselves. “We conduct incremental improvements in our seal designs at our internal test facilities, so we are always progressing. It gives us the ability to present seals to a customer for testing with a higher degree of confidence in the seal’s performance; we make test fixtures that simulate or approximate the customer’s equipment since we do not have the full equipment ourselves,” explained Hedger. “Whenever we deliver their seal, our customer is installing it in their complete equipment. This is where we see if all our hard work, design, and testing paid off. This is the moment when we learn if we fully captured all the criteria for the application. Whenever we get the news from our customer stating that the seal passed, we get extremely excited. Our hard work indeed paid off.”
Adaptability to Timelines
CDI’s initial project kickoff does not last very long before moving through its floating phase. The company speaks with its customers’ engineers to fully comprehend the project’s scope and criteria, such as minimum and maximum temperatures, the maximum pressure, and the number of mechanical cycles the valve will undergo. It then establishes the more concrete details of the project’s design like the gland dimensions where the seals will reside, tolerances, and surface finishes. The company must study all aspects of its customer’s design to determine how the equipment operates and whether modifications are needed to optimize seal performance. “We do all the design reviews, design presentation, and costing. The customer’s project timeline determines how long we have allocated to perform testing. For example, the ISO 15848-1 test with 20,000 mechanical cycles can take one month or longer to complete depending on the speed of the valve’s actuation. Testing on this particular seal lasted a few months, but timelines do vary from project to project. There are projects where a customer may have their equipment already manufactured, so whenever they win a project, all they need is the seals and to test before shipping their valves. Other times the OEM may have to build the whole valve once a project is won. That process typically takes a few months, which was the case with this seal; it gave us the time to conduct additional testing, and our customers really appreciate that,” Hedger detailed.
Oftentimes, the end user will approach CDI’s customer with a particular project that has an explicit completion date. CDI becomes involved and does everything to ensure its customers are delivering their product to the end user on time. The company also helps by providing seals that have undergone pre-testing, which avoids potential delays that can extend a project’s timeline. Having in-house testing capabilities puts CDI at an advantage and allows its customers (the OEM) to meet their own customer’s (the end user) expectations.
“A customer developing an entire new valve requires new sealing apparatus that must work with that valve because it is a custom innovation. We might also have customers that are on the maintenance, repair, and operations (MRO) side that are just looking to replace seals for existing equipment, and so the turnaround time must be a lot faster. The timeline varies by industry, equipment, and application. So, dexterity is a necessity,” said Schoeffler.
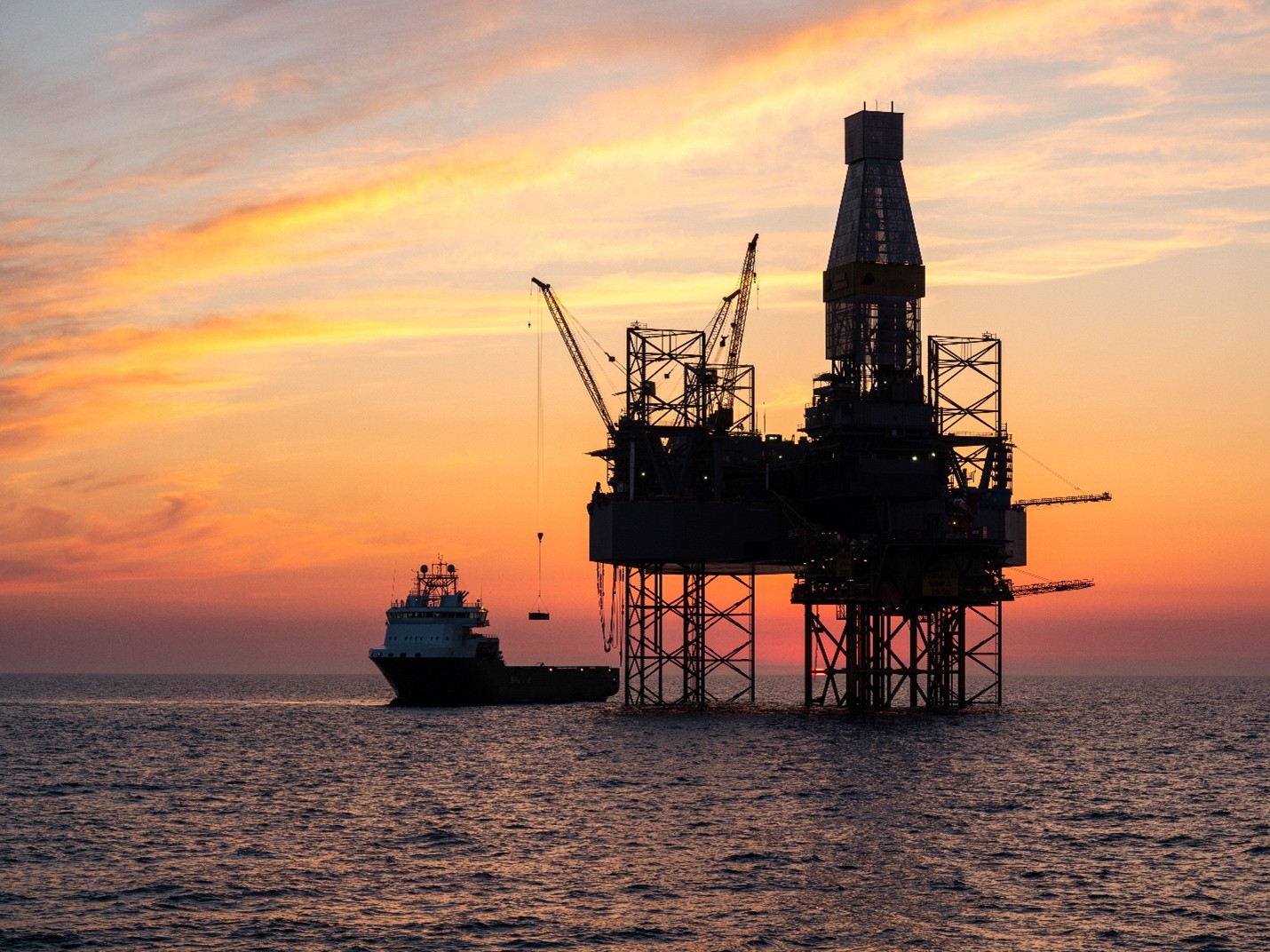
Accepting All Challenges
CDI’s main challenge is the test itself. The company wants to ensure it is providing a solution that fulfills its customers’ requirements and keeps the bad fluids at bay so they do not escape into the environment. “We often have customers approach us in the middle of a project when seals from another supplier are experiencing performance issues. In this scenario, we draw upon our prior experiences and knowledge, integrating our design philosophies to ensure that our seals are compatible with existing hardware, while also developing sealing solutions that are optimized for extreme conditions,” said Ward.
“We like the challenges and the hurdles. It is a mindset that pervades the entire company. When people bring us something that does not work for them, we come together to find a way to overcome the obstacle and make it work, and at the end, we say, ‘That was an adventure!’” added Schoeffler. “Our customers’ wins are our wins. When our customers succeed, we feel their success because we feel like we are part of their company. Every time they say ‘yes’ to working with us, we become a part of their team – every single time. We take that commitment very seriously.”
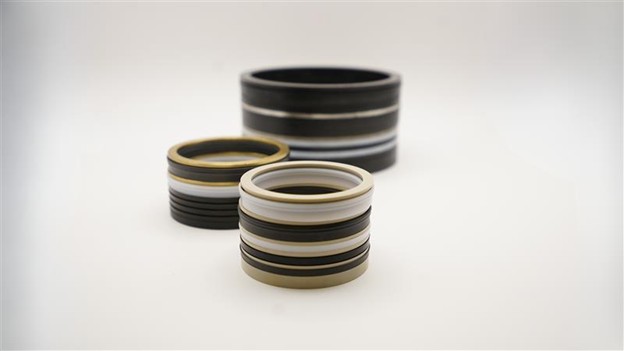
CDI is rightfully proud of the business it has built. Its focus is and will continue to be driven by a philosophy that enforces environmental responsibility and supports its customers. “The whole reason you get into engineering is because you want to solve problems. The more challenging the problem, the more satisfying it feels when you find and share the solution,” Ward concluded.