Storage tanks are used across most industrial operations, from material transport, to onsite facilities for chemical use and storage. The vapors venting from these tanks can be a significant source of fugitive emissions, during the loading and unloading of tanks, interior cleaning, as well as during storage and transportation of the liquid contents. Efforts to mitigate fugitive emissions from tank venting can include the use of control valves, sealing systems, as well as continuous monitoring and detection technologies, emissions capture and reuse technologies, and emission control technology. Before diving into the specifics of how to capture and treat these tank emissions, it is important to first give an overview of assessing emissions.
By Tasha Jamaluddin, Managing Director, Epcon Industrial Systems
Accurately estimating tank emissions allows an operation to determine what EPA regulations and permitting they are subject to and develop an emission control plan to install the proper monitoring and mitigation technology for long term compliance. There are many factors that can affect the quality and quantity of these tank emissions. The chemical makeup of the stored liquid is obviously the most fundamental because it determines the VOC concentrations and potential varieties of emissions produced. However, for accurate calculations and estimations, it is also important to consider the conditions of storage. These include volumes of liquid; turbulence or movement of liquids and standing times; as well as the atmospheric conditions of the tank location, such as above or below ground, altitude, temperatures ranges and wind conditions.
In addition, the tank ‘type’, configuration, and design features can be determining factors for assessing fugitive emissions. While there are about eight different ‘types’ of tanks, the most commonly used type outlined in the following case studies are fixed roof tanks, often utilized for long term storage, as well as for trucking and transport. Additional configurations and design features include the tank dimensions; interior and exterior paint color or metal finishing; roof design, ranging from fixed domed to variable; the inclusion of expandable vapor reservoirs or diaphragms, or bladders; a variety of pressure vents, valves and seals, and many more bells and whistles that can be selected based on application.
Ultimately, the final design and end use of the tank greatly affect the quantity, quality, and pressure variability of vapor emissions produced from the stored liquids, all of which are essential in managing tank emissions during both idle (or standing) loss and active (or working) loss periods.
Every one of these storage tank applications are prone to fugitive emissions, all of which need to be monitored, controlled, and often treated by air pollution control technologies.
Thermal oxidizers are the leading air pollution technology for controlling emissions from industrial processes, including those from tank venting applications. In thermal oxidation, unwanted organic compounds are converted into carbon dioxide and water through high-temperature oxidation. While direct fired thermal oxidizers (DFTOs) are the most basic form of air pollution control, recuperative and regenerative thermal oxidizers provide heat recovery from the VOC thermal oxidation process, which reduces overall energy cost.
The selection and design of a thermal oxidizer system should be determined based on the process stream and the actual chemical composition of the emissions. Additional safety considerations must be implemented to reduce explosion risk and prevent flashback and detonation into and out of the thermal oxidizer and upstream vapor-feed ducts.
The following project case studies describe two different tank venting applications, tank loading and unloading stations as well as tank cleaning operations. These projects showcase how even the same applications that require similar solutions need to be customized to suit the facility layout and operational demands to conserve excessive fuel combustion and deliver a comprehensive long term emission control solution.
Case Studies from Liquid Chemical Distribution Operations
The following two case studies are from chemical distribution facilities with tank loading/unloading terminals. These facilities serve as vital liaisons between chemical producers and transporters, and typically consist of chemicals or petroleum storage tanks and several loading/unloading racks to meet consistent delivery of bulk chemicals to satisfy local demands. These liquid terminal operators must continuously meet strict emissions guidelines while managing various flows of product through their facility tanks, a complex task given the broad range of chemicals and different associated vapor streams.
They also have significant variations between standing losses from idle storage tanks, as well as working losses during the transfer process when the fluid turbulence effect generates excessive airborne vapors. Additionally, these types of operations have been prone to a large number of explosions and accidents, with the potential for a fire to travel and destroy the entire terminal. Therefore, it was imperative to safely capture and destroy the fugitive emissions in the operations to remain compliant with environmental and workplace safety regulations.
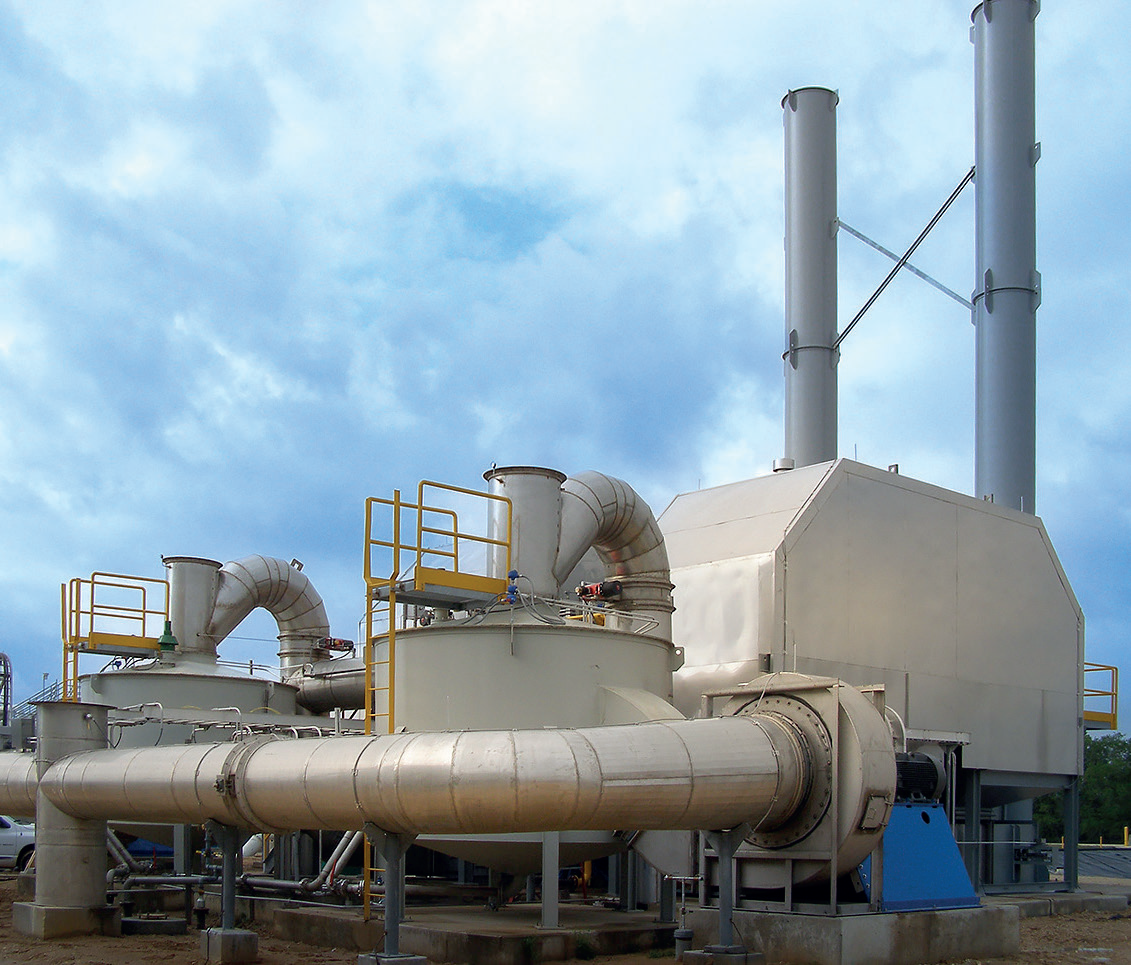
The first application was for a truck terminal that had multiple loading and unloading stations, and needed to control the excess vapors released when the tank trucks were actively being unloaded or loaded. This operation wanted to replace its outdated open flare technology, as it was extremely inefficient and could not guarantee a destruction removal efficiency (DRE) rate for regulatory compliance.
Due to compliance regulations, emission control equipment is required to be in operation all the time, regardless of cost. This significantly impacts the overall facilities’ environmental and financial performance, as excessive fuel is required to operate the emissions control equipment, even during idle periods when there is no loading/ unloading activity taking place and there are significantly lower hydrocarbon concentrations released from tank standing losses.
When designing the system, the primary focus was on optimizing energy efficiency and fuel savings, as well as safety. A single vapor collection tank, also referred to as a bladder tank, was utilized for effective vapor collection from all the storage tanks, container filling stations and loading/unloading racks across the entire terminal operation. The vapor collection tank was incorporated with different position level sensors and pressure measurement instrumentation for effective control and the subsequent release into the emission control system. Depending on the loading and unloading activity and rates, the collection tank offered the new capability to hold vapors up to seven hours.
To replace the open flare, a regenerative thermal oxidizer was engineered, equipped with a high-solvent bypass as a heat release, which automatically detected and increased in capacity for high-concentration vapor, and able to handle the variable fluctuation and higher loading. This flexible design also could achieve better fuel consumption compared to the flare technology because of the high heat exchanger efficiency as well as fuel conservation.
Several features were in place to mitigate any safety concerns and avoid potential shutdown of the thermal oxidizer system in the event of excessive hydrocarbon concentrations being diverted to the oxidizer. The design incorporated flame arrestors to address any potential concerns of flashback from the burner system back to the larger vapor collection tank, as well as flow control mechanisms to limit high concentration overloading into the thermal oxidizer by managing inlet vapor flow rates and mitigating excess vapor from accumulating in the collection tank.
This new design provided an initial capital cost savings, over 50% less than the conventional approach of designing a full capacity emission control device to handle irregular and often infrequent process loads. It also lowered operating fuel cost by allowing the thermal oxidizer to stay in an idle mode, with the exception of the vapor collection tank discharge periods.
A similar application for an expansion at a Texas specialty chemical distribution operation, required a new re-engineered system for tank venting, but yielded a different air pollution control strategy. Similarly, the project challenges included high fuel and operational cost due to fluctuating large volumes of incoming vapors from multiple emission sources and varying concentrations.
Epcon’s experts where on the front end of the project, designing and configuring the vent control strategy and implementation plan across the tanks and distribution terminals, which allowed them to reduce operating cost and provide greater flexibility of the sequencing of their loading/unloading operations. By incorporating a vapor accumulator for each of the tanks, the team was able to significantly reduce the peak loading, allowing for much smaller and more cost-effective thermal oxidizers for the air pollution controls.
To mitigate the risk of storing volatile vapors, a series of blocking valves and temperature monitoring controls were utilized in the design to react in the event of any system malfunctioning, and flashback dangers. Multiple L-shaped direct fired thermal oxidizers were mounted on skids allowing the operator to move the units as needed across the facility. The approach of utilizing multiple vapor collection units within the storage tanks combined with smaller direct fired thermal oxidizer systems resulted in significant cost savings to the chemical distributor while successfully achieving a higher destruction rate efficiency (DRE) for regulatory compliance.
Ultimately, both of these custom-engineered solutions, one with a single vapor collection unit and a large RTO and the other with several vapor collection units at each tank and movable DFTO units, proved to be operationally more efficient based on each facility’s unique demands. This showcases how even the same application and similar solutions need to be customized to conserve excessive fuel combustion and provide a comprehensive emissions solution for the environment and the customers.
Case Studies from Tank Cleaning Operations
A small tank cleaning facility that utilized steam for cleaning the tank interiors, generated noxious emissions from benzene, toluene, and ethylene compounds, resulting in an odorous nuisance to the neighboring community. Additionally, the facility wanted to find a more economical and efficient solution to reduce its wastewater disposal and operating natural gas consumption.
After a complete analysis of the existing process and hazardous compounds, a completely redesigned economical, safe, and reliable system was put in place. The final installation consisted of a pipe network that supplied diluted process gases from across the operations, including from the wastewater and sludge tanks into a single thermal oxidizer, and a waste heat boiler to generate steam for cleaning. The tank cleaning process was modelled as a batch process for wastewater and a dynamic process for the VOC concentration in the gas phase.
Since the volatile emissions came from a wide variety of materials was critical to monitor and dilute any hydrocarbons concentrations below safe explosive levels before entering into the regenerative thermal oxidizer (RTO) system. To address this important safety concern, custom specialized lower flammability limit (LFL) monitors were incorporated in the design to measure flammability levels in the incoming vapors and provide feedback signals to control dilution air volume to achieve fine system controls. As a bonus, the facility went from spending 13.5¢/gallon of wastewater down to 7.5¢/gallon, only producing 2,800 lbs of steam/hr to generating 8,600 lbs of steam/hr.
Additionally, the installed system was able to reduce wastewater by over 5000 gallons/day, saving an estimated $102,000 per year in wastewater treatment alone. The facility eliminated their odor problem, safely diluted the VOCs to 50% of LEL, while also meeting the most stringent EPA regulations by destroying 99.9% of VOC emissions.
A similar application was a project for a tanker truck cleaning operation that needed a mobile air pollution control system that could be moved around the facility based on the trucking demands to handle the fugitive emissions released during the tank cleaning process.
For this project, a mobile direct fired thermal oxidizer (DFTO) for vapor & odor control was used. The 36-foot-long, trailer mounted oxidizer system was fully integrated and included onboard power generation and controls. The mobile unit not only gave the facility the flexibility they needed, but the self-contained unit was also convenient and user friendly.
Again, both of these custom-engineered solutions for similar tank cleaning operations, one with a an RTO and the other with a movable DFTO, have proven to be optimal based on the facilities unique demands.
Conclusion
Both liquid chemical terminals and tank cleaning operations must continuously meet strict emissions guidelines while managing various flows of a broad range of chemicals and associated vapor streams with large fluctuations in volume and VOC content. These case studies outline how similar applications do not necessarily call for similar solutions. The appropriate thermal oxidizer needs to be custom engineered into the overall system to be operationally more efficient. In addition, it is key when designing custom air pollution that accurate estimation techniques are used in determining the proper management of fugitive emissions from tank venting applications to stay compliant and protect the environment and public health.
