Mitigation Efforts Underway
There are a number of ways to reduce or eliminate emissions and many companies take different avenues to address the issue. Some methods require an investment, others deliver a return on investment within a reasonable time, while some methods reduce emissions at no additional investment.
One of the methods that many companies have looked at is recovery systems that recompress seal leakage, inject it back into the pipeline and evacuate the gas from the compressor loop rather than venting it. These systems require investments, and the return is based on fines for excessive emissions or credits for reducing them. While this mitigates emissions, the ideal avenue to follow is to prevent the need to vent a compressor and reduce or eliminate the seal leakage.
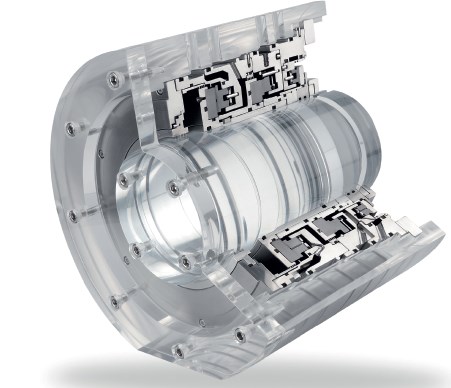
Technology to Mitigate Emissions
Outdated DGS Technology
Dry gas seals (DSG) have come a long way since their first use in compressors, yet many seals with outdated technology are still in use. For example, despite the number of improved options, some seals continue to use Tungsten carbide and carbon face material. These are viable materials when the right seal conditions are provided. The downside to the materials is the higher leakage and failure modes that produce catastrophic seal failures and substantial equipment damage. The silicon carbide used in new seal designs deliver lower leakage by 50 %, or more, and are equipped with a more robust and reliable seal that minimizes consequential damage should a seal failure occur.
Another method of reducing dry gas seal leakage that could be implemented more regularly is grooves geometry. Grooves are etched in the rotating ring face for producing a stiff gas film between the rotating and stationary seal rings for preventing contact during operation. Extensive development work was undertaken to identify the groove geometry effects for reducing leakage and delivering the best gas film stiffness. The ideal grove was identified as a bi-directional unique 3-dimentional geometry. Not only does the groove operate effectively when turned in either direction it also encourages fine debris to pass though the groove rather than collect in it. This ensures the groove retains its effectiveness even when finer particle contamination may be present. Typical groove designs collect the fine debris in the groove, reducing its effectiveness, which leads to seal failures.
The 3-dimensional groove is also more effective when liquids are present between the seal faces. Starting a compressor with liquid in the seal requires substantial torque to break the liquid bond. Often seal failures occur due to these conditions on a restarted. The 3-dimensional groove substantially reduces the torque to break the bond allowing for more reliable restarts.
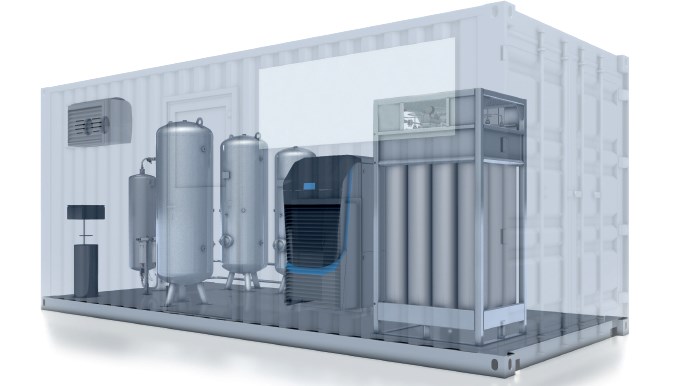
Seal Gas Boosters to Prevent Venting
To avoid venting a compressor loop it is imperative that a clean filtered gas is supplied to the dry gas seals. Liquid and particle contamination from unconditioned process gas often enter the seal gap during a compressor pressurization or while the compressor is in a pressurized standstill condition. These contaminants are detrimental to seal reliability and are the root cause for a large majority of seal failures. To prevent contamination during a stand still condition, the compressor loop is often vented. To prevent venting, seal gas boosters are commonly used. Boosters take unfiltered gas from the compressor and draw it through a conditioning system for providing clean dry gas to the seals. Just as with dry gas seals, newer seal gas booster technology has been developed for delivering an adequate and consistent seal gas supply. The newer electric driven rotary boosters deliver reliability unmatched by the original technology. This new technology allows unlimited pressurized compressor hold. An example of a rotary seal gas booster is the EagleBurgmann RoTechBooster. Providing seal gas to the seals during standstill not only prevents compressor loop venting, but ensures a reliable compressor start.
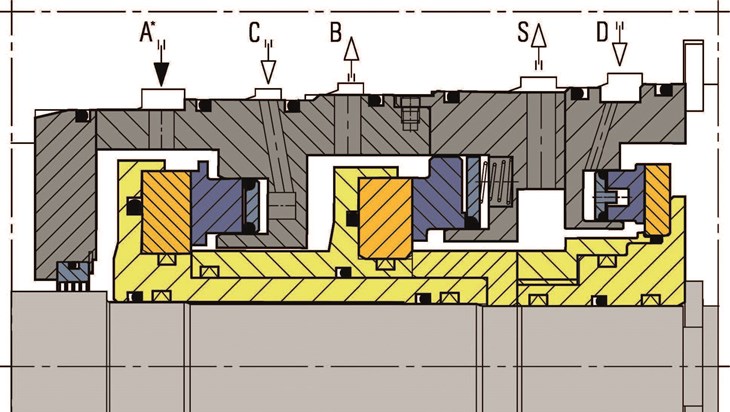
Achieving New Milestones
Reducing seal leakage is a step in the right direction, but the ideal solution is eliminating process gas from escaping through the seal. This can be made possible by using a coaxial separation seal technology and developing the operating philosophy to manage higher pressures for typical pipeline compressors. A coaxial seal works by injecting gas through the stationary seal ring to produce the gap between it and the rotating seal ring.
As the gap between the seal rings is produced by injected gas, it becomes more tolerant of liquids. Injecting the gas this way produces a constant gas flow and along with the 3-dimensional groove, encourages the liquid to pass though the gap with no detrimental effect. Liquids entering a traditional seal blocks the seal gap and gas flow, which leads to heat generation and seal failures. With a continuous gas flow the heat is carried away along with the liquid.
The seal gas to support such as seal design is a fraction of that required for a typical dry gas seal. This makes it much easier to use an external seal supply such as nitrogen. A typical 5” seal operating at 1,000 PSIG requires a 162 SCFM seal gas flow per seal. A coaxial dry gas seal design only consumes 2 SCFM or less. So, providing 4 SCFM nitrogen at 1,008 PSIG becomes a viable option. Providing the seal with clean dry nitrogen, then ensures its reliability, eliminating potential seal failures, and eliminates process gas escaping the compressors.
Cost-Efficient Mitigation
While recompressing seal leakage continues to be used, there is an added cost and payback may take a long time. The better options are using a low leakage seal and a reliable seal gas booster. The ultimate solution to eliminate emissions is with a coaxial seal, like the EagleBurgmann zero emission CobaDGS. For a new installation the capital cost is no different than a typical dry gas seal and system and can be lower when extensive gas conditioning is required. When retrofitting existing seals, there is an investment required, but the cost is quickly recuperated from preventing emissions. This can be shortened even more when fines or carbon credits are calculated into the saving.
ABOUT THE AUTHOR
Benjamin Hellmig is a product manager at EagleBurgmann Germany with 14 years of experience in the field of dry gas seals and systems. In his position he has led and participated in several development projects for compressor and turbine shaft seals. Benjamin is a graduated industrial engineer from the university of applied sciences in Ravensburg-Weingarten, Germany.