In this era of significant growth and heightened focus on environmental concerns, the industrial landscape is undergoing substantial transformations.
Fugitive Emissions Journal had the delight of speaking with Peter Chin, Vice President of Marketing, Final Control Business Group at Emerson, about his insights into the interconnections among operational stability, reduced downtime, technological advancements, and the path toward a more sustainable future.
By KCI Editorial
Career Beginnings
After receiving a degree in engineering, Chin began his professional career working at a British engineering firm, where he actively contributed to new product development, operations, and preventative maintenance across various locations, including the UK, Argentina, Germany, and the U.S. Seeking to expand his expertise, he pursued an MBA at Washington University, and he joined Emerson in 2007.
At Emerson, Chin made significant advances in his career and eventually assumed a leadership role in the Asia Pacific Industrial Regulators Business Unit. This provided the opportunity to relocate to China in the late 2000s, providing Chin with firsthand exposure to the dynamic growth in Asia. “In North America, we have not built a large refinery in decades. In China, I watched the construction of new refineries and petrochemical plants and had the opportunity to get involved from an infrastructure perspective,” he reflected.
Moving back to the United States brought Chin into the Global Industrial Regulators and Tank Management business, as well as the Pressure Relief Valves business. “Last year, I took on the role of Vice President of Marketing in the Final Control Business Group,” relayed Chin. He and his team have the responsibility of effectively communicating expertise to professionals engaged in facility design, construction, operation, and maintenance. Furthermore, they actively seek to establish partnerships to enhance productivity, reliability, safety, and sustainability through innovative valve solutions.
Ramifications of Device Failure
Unplanned downtime happens for several reasons, including activation of one or more of the multiple layers of safety within industrial plants. Numerous safety levels are added or modified as safety measures evolve and grow over time. When an abnormality is detected, certain safety layers are activated, leading the system to “fail safe,” typically in a closed position. This causes an interruption of energy and gas flow. In certain cases, the system may “fail open” to reduce pressure and keep the plant safe. However, this can cause unwanted emissions to be released into the atmosphere.
During a system shutdown, any product present in the system might be wasted, creating financial losses. Additionally, the process of restarting the system consumes a substantial amount of energy, further intensifying the impact of reliability and sustainability. Ultimately, poor reliability has detrimental implications on sustainability, which include financial loss, wasted resources, and heightened energy consumption.
Reliability and Sustainability
When asked about reliability, Chin said, “In a plant setting, reliability means ensuring that the process operates in a manner that yields maximum output with the specific input provided, while maintaining safety. For companies, the ultimate objective is to increase their throughput while simultaneously reducing downtime, energy consumption, waste, and emissions, therefore making reliability very important.”
“A relevant analogy can be drawn in our home HVAC systems on a cold day, where one could raise the temperature by turning up the thermostat, but that would lead to greater energy consumption.” Similar to checking that the windows are shut properly and the effectiveness of window seals to retain heat in a home, a well-functioning plant ensures that all components work well to reduce the need for excessive energy consumption and achieve the desired outcome.
The strong drive towards a higher return on investment (ROI) means the focus should be on building a plant that surpasses the existing ones. “If we want a higher output, we must look at reliability. We want to optimize the process right from the design, and we want to have the best technology so the outcome can be better,” explained Chin. He also commented that back in the 2000s, the topic of sustainability was not as prevalent as now. “However, with the growth in capital investment, industries are now focused on being more efficient and more effective to reduce waste, meet sustainability targets and drive higher ROIs,” said Chin. “I see this as a focus on reliability; to optimize the process design and select the right technologies and partner to work with on projects.”
“I think reliability is one of the important levers for sustainability, but not the only one,” said Chin when asked about sustainability. Another aspect driving sustainability is maintenance. If equipment is not properly maintained, it can result in venting and fugitive emissions, loss of product, and an increase in energy consumption.
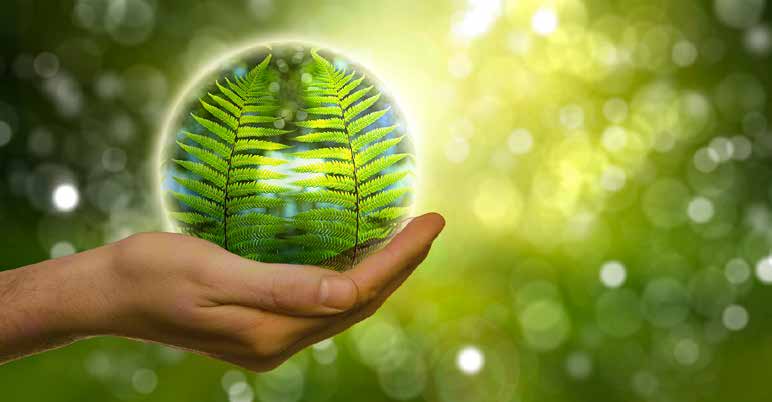
Future of the Industry
When asked about the future of the industry, Chin hopes that the focus will be on reducing emissions and improving monitoring. “Reducing emissions is crucial to preserve the industry for future generations. It is important to attract new talent into the industry with this mindset to push it in the right direction,” explained Chin. “The message of caring for the environment and sustainability will become a big consideration for people as they take up employment.”
When it comes to technological advancements, Chin relayed, “We started with having monitors or devices that alert when something transpires. We would then tell the operator that something in the field needs maintenance or replacement, but only after something has happened. Now, when developing new technology, we are looking at how we can provide insight so that operators can act before something occurs, transforming the way valves interact with the world.”
This is where predictive maintenance comes in. “Monitors that track the trends of how valves operate and provide insights would be helpful for several reasons,” said Chin. “It would help reduce the chance of an event happening in the first place and therefore reduce downtime. It would also help customers figure out what parts need to be replaced, instead of waiting for the equipment to be removed and then inspecting to discover what went wrong. The next step is now thinking about how the right parts or kits can be provided to the operators before the system is down,” added Chin.
Technological advancements are being made in the industry already. “We have new equipment and technology that reduces emissions by improving accuracy when compared to years ago,” said Chin. Venting emissions is one of the many improvements in today’s equipment as it is now done in a controlled and quick manner. Another impressive feat is in the actuators on pipelines. If there is a need to open and close those valves, methane gas will not be emitted into the atmosphere. Instead, the current technology allows the gas to be captured and put back into the pipeline.
“There are multiple things that we are working on that we are able to rethink and redo by pushing the boundaries of technology,” said Chin. “Improvement is always possible, from how tight we can keep seals to how fast the devices can react to specific conditions; new ways of thinking are the key,” concluded Chin.