Promulgated by EPA in 1981 and codified in federal and state air quality regulations, Method 21 requires the use of a specialized VOC analyzer. The type of analyzer is left up to the user, provided it meets Method 21 requirements. For instance, the analyzer must be portable, have a bat-tery-powered sample pump, be certified intrinsically safe, and equipped with a sample probe no larger than ¼-inch in diameter. When monitoring a component, the analyzer’s probe tip must remain in contact with the component’s potential leak areas (except for moving equipment such as pump shafts), and a complete circumference of each potential leak area must be made.1
How Long Does Method 21 Take and How Often Must it be Done?
Method 21 inspection times vary with component type and size, ranging from 15 seconds for small components up to several minutes for larger ones. If an elevated reading is measured on a component, then the inspector must continue monitoring there for a longer period of time, to ensure the concentration does not rise above the component’s leak threshold. An experienced Method 21 inspector is able to monitor between 250-450 valves per day on average. A typical refinery or chemical plant, containing many thousands of valves, pumps, and connectors in VOC service, requires a team of monitoring inspectors to complete the routine Method 21 monitoring on schedule.
LDAR programs are typically contracted out, with the LDAR contractor pro-viding the monitoring team, as well as the hardware and software needed to complete and report the monitor-ing results. For some of the larger facilities, as many as ten or more monitoring inspectors are needed to complete the Method 21 monthly and quarterly monitoring required by federal and state regulations.
Is Method 21 Effective?
If done properly, Method 21 is very effective at identifying leaking components. Various factors combine, however, to make routine Method 21 leak detection ineffective. LDAR contractors work in a highly competitive market resulting in low wages, low hiring standards, and high turnover rates. Method 21 inspectors must work in a noise-filled, dangerous environment, at elevated heights, and in all types of weather. The work is challenging, the pay is low, and monitoring hundreds of components day after day quickly becomes monotonous. As a result, LDAR Method 21 programs are prone to significant monitoring in-consistencies2, as demonstrated by the following two studies.
In 1994, EPA’s National Enforcement Center (NEIC) conducted Method 21 audits at 14 refineries across the nation. The percent leak rates found by the NEIC inspectors were, on average, four times higher than that reported by the facilities. The study’s investigative report concluded that VOC com-ponent inventories were inaccurate, monitoring procedures were incorrect or inconsistent and that, in particular, Method 21 procedures were not being followed.3
Another study completed at a Texas refinery in 2007-2008, consisted of two facility-wide infrared (IR) camera surveys, the first imaging only LDAR program components, the second im-aging all components. Although the refinery had a mature LDAR program, even so, in the first pass through the refinery in which only LDAR components were imaged, an additional 158 previously unreported regulatory leaks were identified by the IR camera, most exceeding 100,000 parts-per-million-volume (ppmv). The second pass through the refinery with the aim of IR-imaging all components, identified 157 new VOC leaks, over half of which were on equipment not traditionally included in the LDAR program, with one leak resulting in an immediate process unit shutdown.4
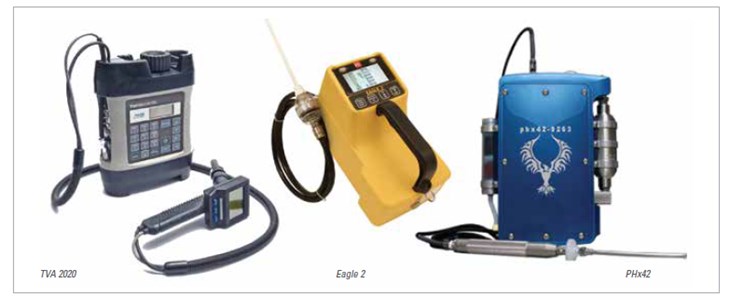
In a typical refinery, having more than 200,000 regulated components, a Method 21 LDAR program’s cost can easily exceed one million dollars per year.5 Unfortunately, studies indicate that most of this money is spent monitoring components that are not leaking.
A 1997 study, for instance, by the American Petroleum Institute (API) at 7 Los Angeles refineries over a period of 5.5 years found that over 90% of the fugitive leaks came from only 0.13% of the components monitored, with only a small number of those being responsible for the majority of the mass emissions. The study’s report concluded that a more efficient method for fugitive emissions monitoring would more cost-effectively find these leaks.6
Another study at five natural gas facilities in 2004-2005 determined that only 2.4% of all monitored equipment was found to be leaking.7
It has been evident for some time that maintaining a team of Method 21 inspectors to monitor entire populations of components only to identify just the few responsible for the majority of emissions, is both inefficient and unproductive. There must be a better way.
Is There a Better Way?
A cost-effective and efficient alternative to Method 21 has been available since 2005, when the FLIR GasFindIR® camera became commercially available for leak detection. Since then, continuing advances in IR camera technology have led to highly sensitive IR cameras that are able to quickly and accurately visualize fugitive emissions. Regulatory acceptance of Optical Gas Imaging (OGI) as an alternative to Method 21 has been following suit.
Industry complaints about the cost and inefficiencies of LDAR programs based upon Method 21 led to the promulgation by EPA of the Alternative Work Practice (AWP) in December 2008. Dubbed ‘Smart LDAR,’ the AWP allows LDAR programs to use OGI in lieu of Method 21. The AWP re-quires monitoring of all components with OGI technology on a monthly, bi-monthly, or semi-quarterly frequency depending on the chosen detection sensitivity level.8
Industry response to the AWP was initially enthusiastic. However, concerns were raised during the review stage about OGI’s ability to detect small leaks. In response, EPA added the requirement that all accessible components be monitored annually using Method 21. This dual requirement to purchase an expensive infrared cam-era while still maintaining an even more expensive Method 21-based LDAR program, resulted in an almost complete lack of interest by industry.
Since then, several regulations have been introduced, approving the exclusive use of OGI as an alternative to Method 21:
• In 2012, EPA proposed in its Nation-al Uniform Standards, the use of OGI technology in lieu of Method 21.9 However, the Uniform Standards has yet to be promulgated.
• In 2014, Colorado released Regulation Number 7, allowing operators in the state’s oil and natural gas sectors to use exclusively one of the Approved Instrument Monitoring Methods for leak detection including either OGI or Method 21.10
• In 2015, in NSPS Subpart W, EPA listed several leak detection methodologies approved for the detection of greenhouse gas (GHG) emissions from petroleum and natural gas production facilities, with annual OGI being listed first.11
• In 2016 Quad Oa was promulgated by EPA for the Oil and Gas up-stream industry, significantly recognizing OGI as the “Best System of Emission Reduction” (BSER).12
The exclusive use of OGI for leak detection has not yet been extended to those facilities with the largest LDAR programs – refineries, chemical and petrochemical plants. These facilities still must maintain expensive, com-plex, Method 21-based LDAR pro-grams, despite studies indicating that OGI is more efficient, more economical, and provides better emission re-ductions. Fortunately, this is expected to soon change with the upcoming release of Appendix K by EPA in the latter part of 2021.
Appendix K is expected to do what industry oil refiners and chemical producers hoped the 2008 AWP would do – permit the exclusive use of OGI for routine leak detection as an alter-native to Method 21.
What Will Appendix K Look Like?
Appendix K is expected to allow the use of OGI exclusively for the detection of fugitive emissions from stationary sources, and we are told that it will include OGI requirements similar to those of Quad Oa, yet will be more specific in certain areas such as initial and on-going operator verification, camera capabilities and sur-vey procedures including the monitoring of all components.13 So, what are Quad Oa’s OGI requirements? A summary is provided below.
How Will Appendix K Change Traditional LDAR Programs?
If as expected, Appendix K accepts OGI as an exclusive alternative to Method 21, the effect upon traditional LDAR programs will be significant. Method 21 analyzer inventories will largely be replaced by several OGI cameras. Teams of monitoring technicians will be reduced to a few professionally trained infrared thermographers. All components within a process unit, including components currently considered difficult and unsafe to monitor, will be surveyed by thermographers in one to two days. LDAR program costs will be cut by 15-30%, and large leaks, responsible for the majority of emissions, will be identified and repaired faster, resulting in significant reductions of annual emission rates.
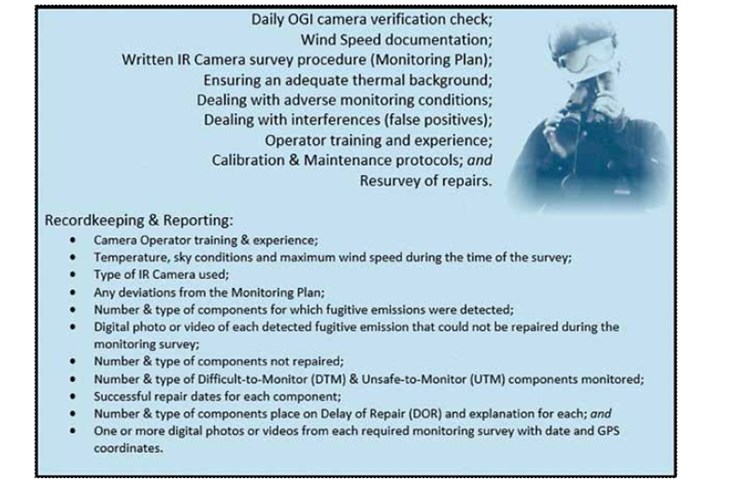
Since first becoming commercially available, OGI cameras have been equipped with cooled IR detectors providing them with the sensitivity needed to visualize equipment leaks. New technological advances now make it possible for uncooled OGI cameras like the FLIR GF77® or the Sensia Caroline Y® to function much like cooled cameras but at a significantly lower cost. Software, provided either as an add-on or integrated in the camera, can now determine mass leak rates, virtually eliminating the need for follow up Method 21 inspections or the use of overly conservative emission factors.
In Summary
Is Method 21 indeed doomed? The answer is, “PROBABLY — but not for a while and not completely.” Method 21 will certainly remain the mainstay leak detection method for smaller LDAR programs as well as for specialized ap-plications in the years to come. But as the prime leak detection methodology for the larger LDAR programs at refineries, and chemical and petrochemical facilities across the country, its doom is inevitable. As indicated, the soon to be released Appendix K, combined with the significantly reduced costs of an OGI-based LDAR program, and the ongoing advances in OGI technology, promise to make this so.
References
1. EPA Method 21—Determination of Volatile Organic Compound Leaks, Federal Register, Vol. 65, No. 201.
2. LDAR Case Study Comparison of Conventional Method 21 vs Alternative Work Practice (Optical Gas Imaging); https://www.epa.gov/natural-gas-star-program/ldar-case-study-comparison-conventional-method-21-vs-alternative-work.
3. Summary of NEIC Leak Detection and Repair Program Investigations, EPA-330 / 9-94-001, January 1994.
4. OGI Through the Years, EPA Optical Gas Imaging Workshop, November 9-10, 2020, https://www.epa.gov/sites/default/files/2020-12/documents/ogi_through_the_years.pdf.
5. Refinery Evaluation of Optical Imaging to Locate Fugitive Emissions, Journal of Air & Waste Management Association 2007.
6. Analysis of Refinery Screening Data; Publication No. 310; American Petroleum Institute: Washington, DC, 1997.
7. Cost-Effective Directed Inspection and Maintenance Control Opportunities at Five Gas Processing Plants and Upstream Gathering Compressor Stations and Well Sites; U.S. Environmental Protection Agency Natural Gas STAR Program; March 2006.
8. Alternative Work Practice to Detect Leaks from Equipment; 73 FR 78199, December 22, 2008.
9. National Uniform Emission Standards for Storage Vessel and Transfer Operations, Equipment Leaks, and Closed Vent Systems and Control Devices; and Revisions to the National Uniform Emission Standards General Provisions; 77 FR 58, March 26 2012.
10. Control of Ozone via Ozone Precursors and Control of Hydrocarbons via Oil and Gas Emissions; Regulation Number 7; 5 CCR 1001-9.
11. Monitoring and QA/QC Requirements, Code of Federal Regulations, Title 40, Chapter I, Subchapter C, Part 98, Subpart W §98.234.
12. Oil and Natural Gas Sector: Emission Standards for New, Reconstructed, and Modified Sources; 81 FR 35823; June 3, 2016.
13. Email from G. Garwood, EPA Measurements Division to the Author (January 26, 2021).
14. Subpart OOOOa—Standards of Performance for Crude Oil and Natural Gas Facilities for which Construction, Modification or Reconstruction Commenced After September 18, 2015; 81 FR 35898, June 3, 2016.
15. LDAR Case Study Comparison of Conventional Method 21 vs Alternative Work Practice (Optical Gas Imaging); https://www.epa.gov/natural-gas-star-program/ldar-case-study-comparison-conventional-method-21-vs-alternative-work.
About the Author
David Ranum is a senior project manager with TRICORD Consulting, LLC. He is an LDAR Subject Matter Expert having spent over 20 years auditing LDAR programs, conducting emission studies, providing LDAR training classes, and attending and presenting on LDAR topics at conferences. David also has a keen interest in infrared technology. He is a Level III Thermographer, works on IR camera-related projects and provides Level I OGI class instruction.
Images Courtesy of RFS Compliance Solutions.