Recent environmental standards are encouraging companies in the industry to regulate operations in hopes to achieve emission-free production in the next few decades. Fugitive Emissions Journal had the pleasure of speaking with Glenn Long, a HES (Health, Environment, and Safety) professional regarding the efforts made to identify and mitigate emission leaks.
By KCI Editorial
After earning his required certifications and ratings, Long was employed as a flight instructor for seven years. He went on to earn a bachelor’s degree in Environmental Geography and minored in Cartography, and then began his journey with Marathon Petroleum Company as an HES Professional 16 years ago at its Canton, Ohio facility. “After working for our Ohio facility for seven years, I relocated to our Texas facility (Galveston Bay Refinery), where I have been employed for 9 and a half years now,” he said. While he has spent some time dedicated to different roles, today, he specializes in the environmental aspects of petroleum refining as a HES professional. Long is responsible for managing a variety of programs within Marathon Petroleum related to regulatory air provisions; one of three major sectors within HES.
Overseeing seven different programs aimed to control air emissions, Long and his team are focused on mitigating the negative effects of fugitive emissions. “My involvement in each of these programs primarily consists of maintaining regulatory compliance in the areas of monitoring/inspections, repairs, and reporting on applicable equipment and components. This includes managing a team of over 40 contractors who conduct much of the required monitoring.” The Texas facility is known for its significant size and complexity and maintaining compliance within each of the Environmental programs is essential to the success of the refinery as a world class facility.
Controlling Air Emissions
While there are several additional programs currently in operation at Marathon Petroleum, the seven programs Long oversees include: the Ozone Depleting Substances (ODS) program, the LDAR program, the Cooling Tower program, the Tanks program, the RSR MACT APRD program, the RSR MACT Benzene Fence-line Monitoring program, and lastly, the HON program.
“Each program has a specific set of requirements and a defined purpose, and it is our job to ensure each are successful and we maintain compliance with the applicable state and federal rules and, in many cases, permit conditions,” stated Long. “For example, our LDAR program generally consists of monitoring, repair, recordkeeping, and reporting requirements. Each of these four areas may have some similarities when comparing the regulatory requirements for them. However, there can be minor differences between the variety of rules and permit conditions as well, and all must be adhered to in order to maintain compliance within the program as a whole.”
Ozone Depleting Substances (ODS)
The ODS rule is designed to regulate and restrict usage of various ozone-depleting gases, primarily in HVAC equipment, in all sectors of the industry. This has been mainly completed through production, import and usage phase outs. Like most programs, there are maintenance, recordkeeping and reporting requirements that must be adhered to. At the Galveston Bay Refinery, Long explained, “We use and maintain a database that houses all our refrigerant units and maintenance records. We have a dedicated site manager in our Maintenance group who is responsible for maintaining all the required records and keeping the database up to date. New units being brought on site are evaluated through the MOC (management of change) process and action items for review are assigned to applicable personnel to ensure compliance with the rule is achieved. My role within the program is to submit reports as necessary and to work with the site manager on evaluating equipment being brought on site to ensure it is compliant.”
LDAR Program
The Leak Detection and Repair (LDAR) program is one of the site’s most complex programs, due to the number of components and the variety of state, federal, and permit requirements that the site complies with. “The site’s LDAR program has in excess of 660,000 components.
Many are required to be monitored on monthly, quarterly, or annual frequency, depending on component type, regulatory requirements, and other nuances. Therefore, our LDAR contractors are conducting monitoring daily and average 90,000 plus monitoring events per month,” explained Long “In addition to the required Method 21 monitoring, we frequently employ the use of Optical Gas Imaging (OGI) infrared cameras and other technologies as part of proactive inspections to detect fugitive emissions from potential sources.”
Cooling Towers
In a refinery, the cooling towers are used to absorb process heat through flowing water to cool fluids and are predominately used to process water for reuse. The site Cooling Tower program utilizes the LDAR program contractors to monitor 25 sample spots on 16 cooling towers for leaks, no less than monthly, pursuant to Appendix P and using a modified El Paso board. In addition, they also collect TDS (total dissolved solids) weekly for several of the site cooling towers as required by site permit conditions. By driving and prioritizing maintenance, operators can mitigate the risk of leaks in heat exchange systems, which is a crucial step towards reducing leak emissions by shortening repair times. The site has a robust find and fix process led by operations and they are heavily involved in locating and isolating the source of emissions in a timely fashion when leaks are found.
Tanks Program
Long has over 12 years of experience in the Tanks program between his time at Marathon’s Ohio facility, and the Texas facility. This has included both the administrative side and field inspections sides of the program. “During my time in Canton, I not only managed the program, including recordkeeping/reporting, but I also conducted most of the required visual and physical seal inspections for the site,” Long stated. “The Galveston Bay Refinery has considerably more floating roof storage tanks and the required inspections are coordinated and completed by our Inspections group.
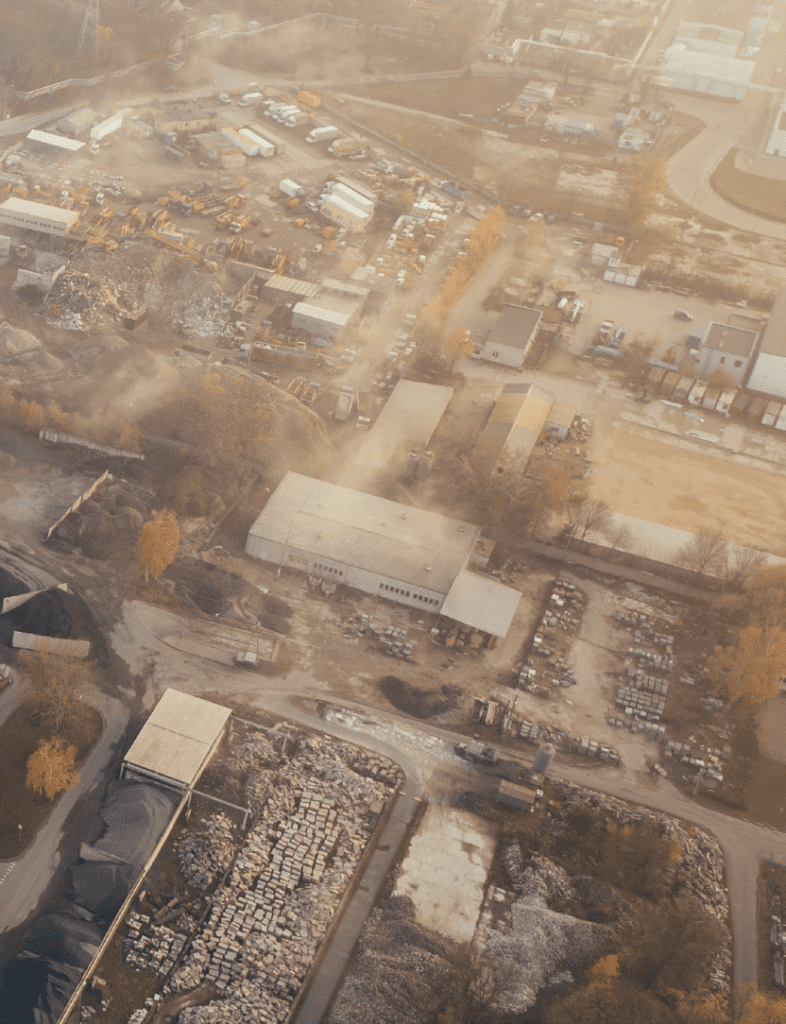
As storage tanks can be a major source of emissions if there are defects in the emission control devices, and can impact other Environmental programs and refinery operations, our Inspections group is heavily involved in ensuring that timely repairs are completed when deficiencies are found.” Long continued, “One of the proactive measurements we are taking is coordinating OGI inspections during physical seal inspections to assist the inspectors with finding areas of emissions concerns while they are performing their physical and visual checks on the seals and deck fittings. This can aid in remediating issues that are in infancy before they become systemic problems, or in finding potential defects that may not be found with the naked eye.”
RSR MACT APRD Program
The APRD (atmospheric pressure relief device) portion of the RSR (refinery sector rule) MACT updates is, essentially, enhanced LDAR monitoring for pressure relief devices in organic HAP (hazardous air pollutant) service.
While primarily designed for pressure relief valves that vent to atmosphere, the updates included Bellows and Pilot-operated RV monitoring, recordkeeping, and reporting requirements. While many of these types of RVs may vent during relief events to a flare or other control device as their primary route, they typically have a ‘bug vent’ or Bellows vent that vents to atmosphere and not to controls.
The equipment leak standards section of the rule now accounts for these atmospheric vents and their potential for emissions during a venting scenario. There are some exemptions for RVs under the rule, including RVs that are completely controlled and do not have the potential to emit to atmosphere. For RVs subject to RSR MACT, RCAs (root cause analysis) and corrective actions may need to be initiated after release events. As Long stated, “My involvement with this program is managing the contractors who conduct the monitoring, ensuring monitoring is completed as recommended and required, maintaining required records, and reporting release events and leak scenarios as needed in the semi-annual reports.”
The Benzene Fence-line Program
This program is also part of RSR MACT updates and requires the placement of passive diffusion tubes around a refinery’s perimeter. The tubes remain in the field for two weeks and then are collected and sent to an off-site lab for analysis for benzene content and new tubes are deployed. The regulatory action level is 9.0 μg/m³ on a rolling annual average. If a site exceeds the action level, they are required to conduct an RCA and implement a corrective action plan as necessary to find/mitigate benzene emissions to below the action level.
The program has become heavily scrutinized by regulatory agencies and Marathon is committed to taking the necessary steps to ensure compliance. “Our site maintains 48 regulatory required sample stations and has several other stations we utilize for troubleshooting. Our LDAR contractor collects and deploys the tubes each two-week period and are heavily utilized in investigating potential sources of benzene emissions as needed,” Long stated. “We utilize a variety of technologies, both reactively and proactively, to help locate benzene problem sources. These include, Method 21 monitoring, UltraRAE devices designed for benzene monitoring, handheld OGI cameras, SPODs used for VOC detection, eGCs (gas chromatographs) and we are currently in the process of implementing a drone inspection program for storage tanks that will utilize an OGI camera. Our Operations and Maintenance groups are also very engaged in the find and mitigate process.”
HON Program
The final program that Long oversees is a federally regulated program that is designed to control emissions from applicable heat exchange systems, maintenance and process wastewater, storage tanks, process vents, transfer operations, and LDAR components. Long explained, “Our site currently has one process unit and several downstream storage tanks subject to the HON provisions. Required LDAR monitoring is conducted by our site contractor and required storage tank inspections are handled by our Inspections group and their contractors. In addition to periodic wastewater sampling and overseeing our LDAR monitoring, I handle the required recordkeeping and reporting for the program.”
Monitoring the Connectors
In addition to understanding the importance of managing and maintaining the integrity of the Environmental programs, Long shed light on the importance of connector monitoring. As valve and connector leaks, among other component leaks, are common, connector monitoring can mitigate the risk of fugitive emissions when it is done proactively.
“At our site, connector leaks outnumber many other component leaks we see. This is likely due, in part, to the sheer number of connectors that we have at the site,” Long explained. “We have several connector monitoring requirements based on regulatory provisions and permit conditions. Therefore, we monitor many of our unit connectors on a monthly or annual frequency, depending on what is required by rule or permit.” He added, “We also do routine connector monitoring in other areas of the refinery that do not have connector monitoring requirements. This proactive monitoring can help in other program areas, such as fenceline monitoring, and has resulted in finding leaks on components that we might not have known existed before.”
The environmental standards that have been proposed across the industry require compliance towards regulations. Long explained his positioning with compliance management as an industry professional; “In my experience, and after speaking with other industry professionals who have taken part in projects overseas, the U.S is certainly more regulated than many other countries. I think the monitoring standards created are, in part, based on the innovation and technology made available to each country, and we are fortunate to be able to actively implement these monitoring technologies in our processes,” he stated.
What To Expect
Drawing on the extensive experience he has gained in the oil & gas industry, Long shared his thoughts of what to expect in the future, as the industry heads towards a transitional period.
“Although, at times, complying with mandated standards can be challenging, I believe Marathon Petroleum continues to make the necessary changes that will lead to influence and action for a sustainable future,” stated Long. “Finding and utilizing alternative energy resources will have a significant impact in the future and I believe it is a strategy that more and more companies like ours will adapt to through modifications of processes and thinking going forward.”
“Consumerism must be kept up with and there are still many functional products, technologies, and practices that rely on petroleum products and resources. However, I expect that the green energy push will continue into the future. In part, this is dependant on consumer support and current and future legislation. As an industry, we must continue to make reliable products in the safest way possible. From an Environmental perspective, this includes managing our programs over and above regulatory standards and reducing/eliminating emissions to create a safer and healthier environment for everyone,” concluded Long.