Fugitive emission reduction has become a high priority goal for virtually every process plant and facility worldwide. Increasingly stringent government regulations, aggressive code enforcement, and corporate environmental, social, and governance (ESG) initiatives have put a strong focus on eliminating these types of unintended releases. However, these improvements must be accomplished with limited operating and capital budgets.
Often the valve technology itself can have a major impact on fugitive emissions, as well as the life cycle costs of the equipment. This article describes a methodology for identifying problem areas and offers solutions for addressing these and other issues.
By Bhavana Gundaboina, Senior Product Marketing Manager, Emerson
A Pressing Mandate
The global focus on fugitive and greenhouse gases has resulted in a host of new and more restrictive regulations. These mandates are also being enforced more strictly, with frequent inspections and large penalties being levied on those companies who fail to comply. Adding to the pressure are the demands of investors and stakeholders, who now insist that companies engage in environmental improvements and show their progress. In response to the latter point, the U.S. Security and Exchange Commission created reporting guidelines so companies can provide consistent and accurate accounts of their ESG programs.
Plant personnel are challenged with meeting these requirements within a limited capital budget, while minimizing operational and maintenance cost impacts.
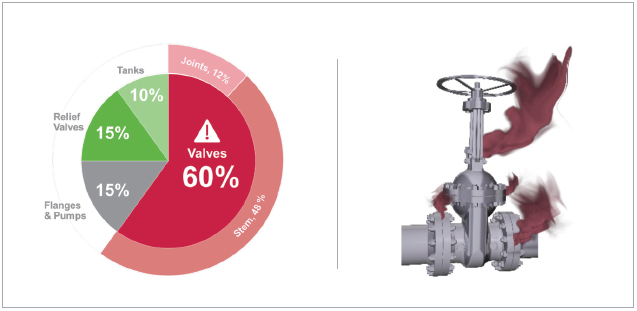
Identifying the Problem
The first step to achieving emission reductions is to understand the sources. Surprisingly, one of the largest sources of fugitive emissions in plants is associated with valves (Figure 1).
Since valves are a significant source of fugitive emissions, they have become the focus of many governmental regulations, and the allowable leakage rates have been reduced in recent years. For instance, the U.S. Clean Air Act Amendments by the Environmental Protection Agency dropped the allowable leakage rate limits from 500 to 100 parts per millions (ppm), and even 50 ppm in some cases.
The costs of these emissions are multifaceted. Obviously, every pound of product that escapes is money lost, but this cost includes not only the raw material cost, but the time, energy, and resources that have already been expended to produce the product. Fines for regulation violations can be significant, and these costs balloon quickly for repeat offenders. Less obvious are the increased maintenance and operating costs associated with poorly performing leak detection programs (Figure 2).
Taken in combination, the cost of fugitive emissions can be extremely high, and leaks of lethal materials add operator and community safety concerns to that list.
Historically, plants have tried to address these problems in a number of ways. One method is to simply sample and test valves more frequently, looking for developing leaks and addressing them quickly. This is effective but expensive, requiring more resources to both test and repair the valves.
Some plants have taken the time to evaluate the cause of the leaks and possibly upgrade the packing design. This costs a bit more in the short term, but usually pays for itself with reduced inspections and longer service life. Packing upgrades can limit fugitive emissions, but in some instances the valve design itself limits the effectiveness of the packing.
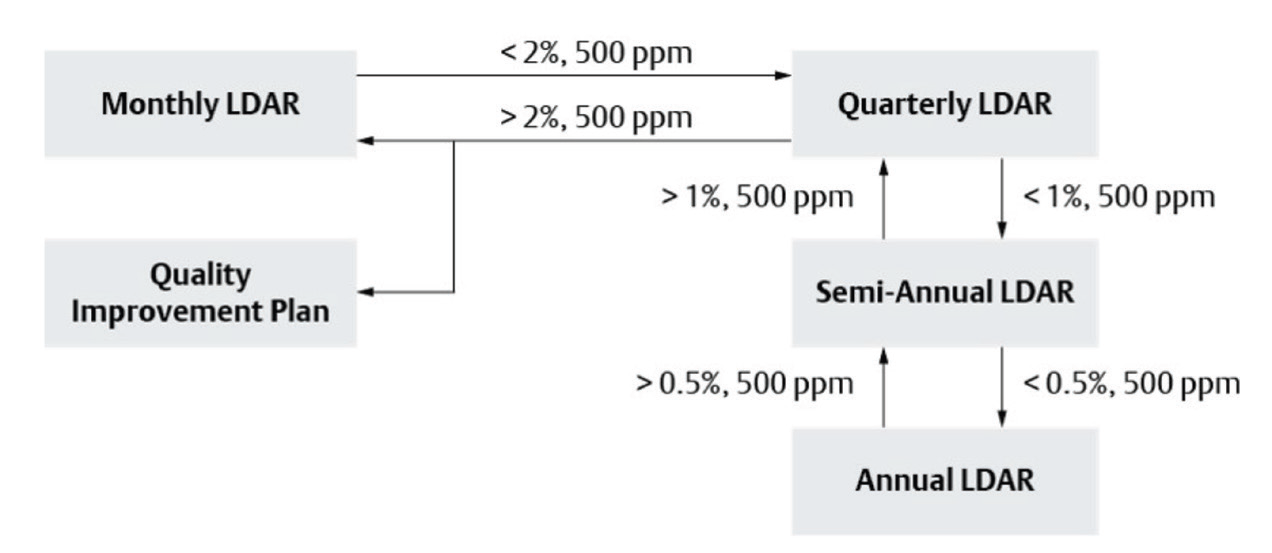
Better Design Alternatives
As Figure 1 shows, the bulk of valve emissions come from the valve stem packing, which has a very difficult duty to perform. It must contain the process and avoid leaks, yet still allow the valve stem to move freely. This is a design challenge for any valve, but it is particularly difficult with a rising stem valve that cycles up and down repeatedly.
With each stroke, the packing tends to wear along the stem, allowing process media to escape. This is particularly troublesome on valves that also encounter pressure and temperature swings. There are improved packing designs that can reduce these emissions and extend maintenance cycles, but inherently a rising stem design is difficult to seal consistently.
From a sealing perspective, a quarter turn valve (Figure 3) has distinct design advantages. Since the valve stem makes a comparatively shorter 90-degree rotation, rather than reciprocating up and down, it tends to wear more slowly. Additionally, any scoring of the packing caused by particulate trapped against the stem occurs horizontally. In rising stem designs, this scoring occurs vertically through the packing rings, which can create a direct leak path to atmosphere, resulting in substantially more leakage.
The Offshore and Onshore Reliability Data Project has estimated that 90% of valve fugitive emissions can be eliminated by upgrading rising stem valves to a quarter turn design. However, there are a number of design improvements that allow some quarter turn valves to outperform others, while providing significantly reduced emissions, as well as a longer service life. Quarter turn valve selection should start by looking for these features.
The packing design directly impacts valve emissions. Recent advances in materials and engineering designs have yielded dramatic improvements in emission reduction (Figure 4). These packing designs utilize spring-loaded washers to continuously compress the packing seals, paired with a combination of different packing ring materials to achieve extremely low leak rates of less than 100 ppm. New packing designs also incorporate special coatings and special valve stem materials to provide long life and smooth movement.

Other design features include precision machining of both the packing components and the valve body flanges. These tight tolerance surfaces are combined with carefully selected engineered materials that have similar thermal expansion properties. This allows the seal to achieve low leak rates, even during temperature and pressure cycling conditions.
In remote oil & gas applications, the actuator and positioners can also be significant source of fugitive emissions when natural gas is used as a motive force. In these situations, advanced low bleed or zero bleed actuators can be employed to minimize or eliminate leakage.
Focus Resources
While a wholesale conversion of rising stem to quarter turn isolation valves could certainly reduce plant emissions, it would require significant capital. Therefore, plant personnel are wise to channel their efforts and resources to upgrade those valves that provide the best payback. These valves are usually found in applications with one or more of the following characteristics:
- Frequent cycling, valve sealing components tend to wear more rapidly and experience consistent fugitive emission problems.
- Thermal cycling, the various components in a valve typically have different coefficients of thermal expansion, so leak paths will emerge and result in emissions.
- Lethal or corrosive service, leaking valves in these applications must be resolved immediately. Bellows seals can drop lethal emissions to zero, while corrosive applications can be addressed with carefully selected materials of construction.
- Criticality, any valve that is critical for plant throughput should be evaluated for its emissions performance to prevent a breach of compliance from taking plant capacity offline.
- Accessibility, valves installed in remote or hazardous locations should be prioritized for upgrade to reduce the burden on maintenance teams to monitor and repair.
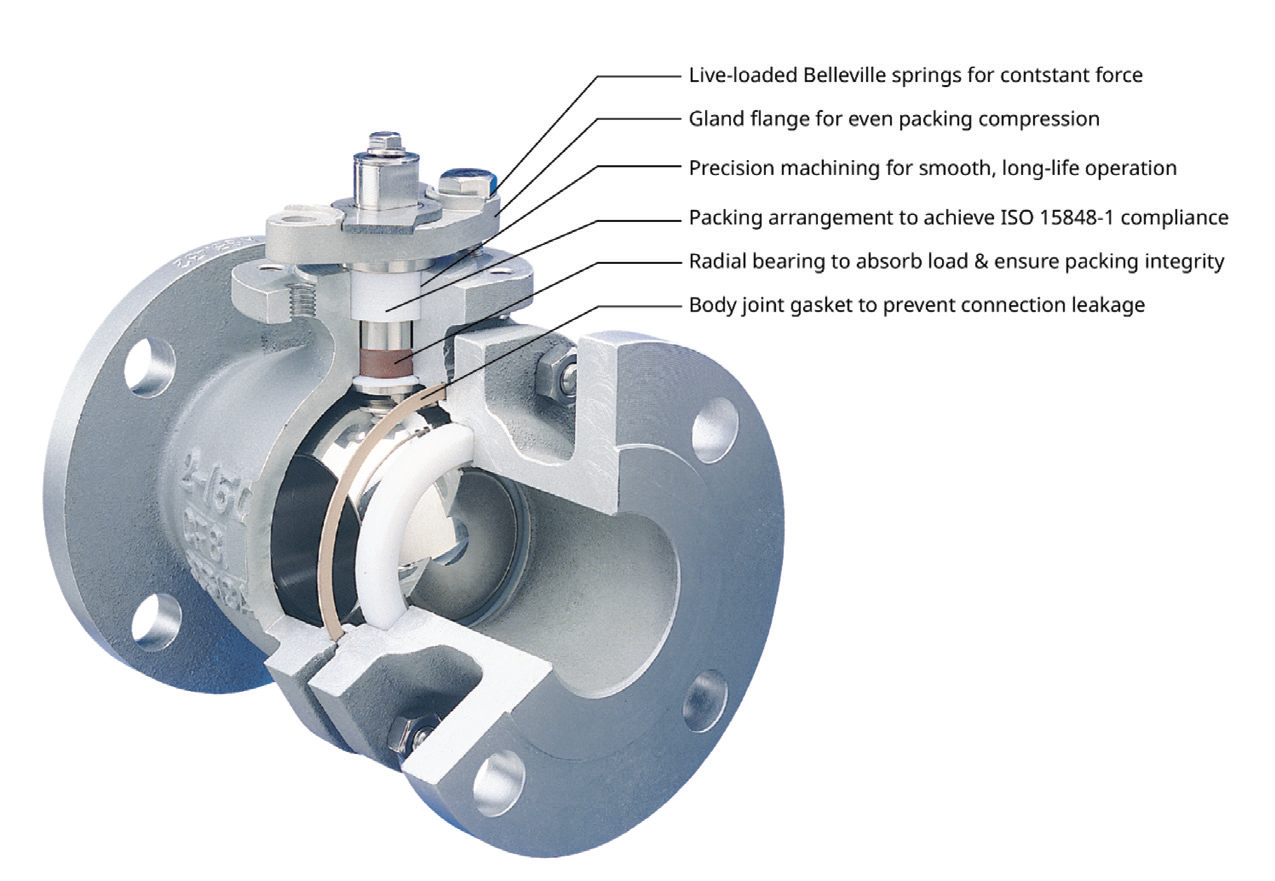
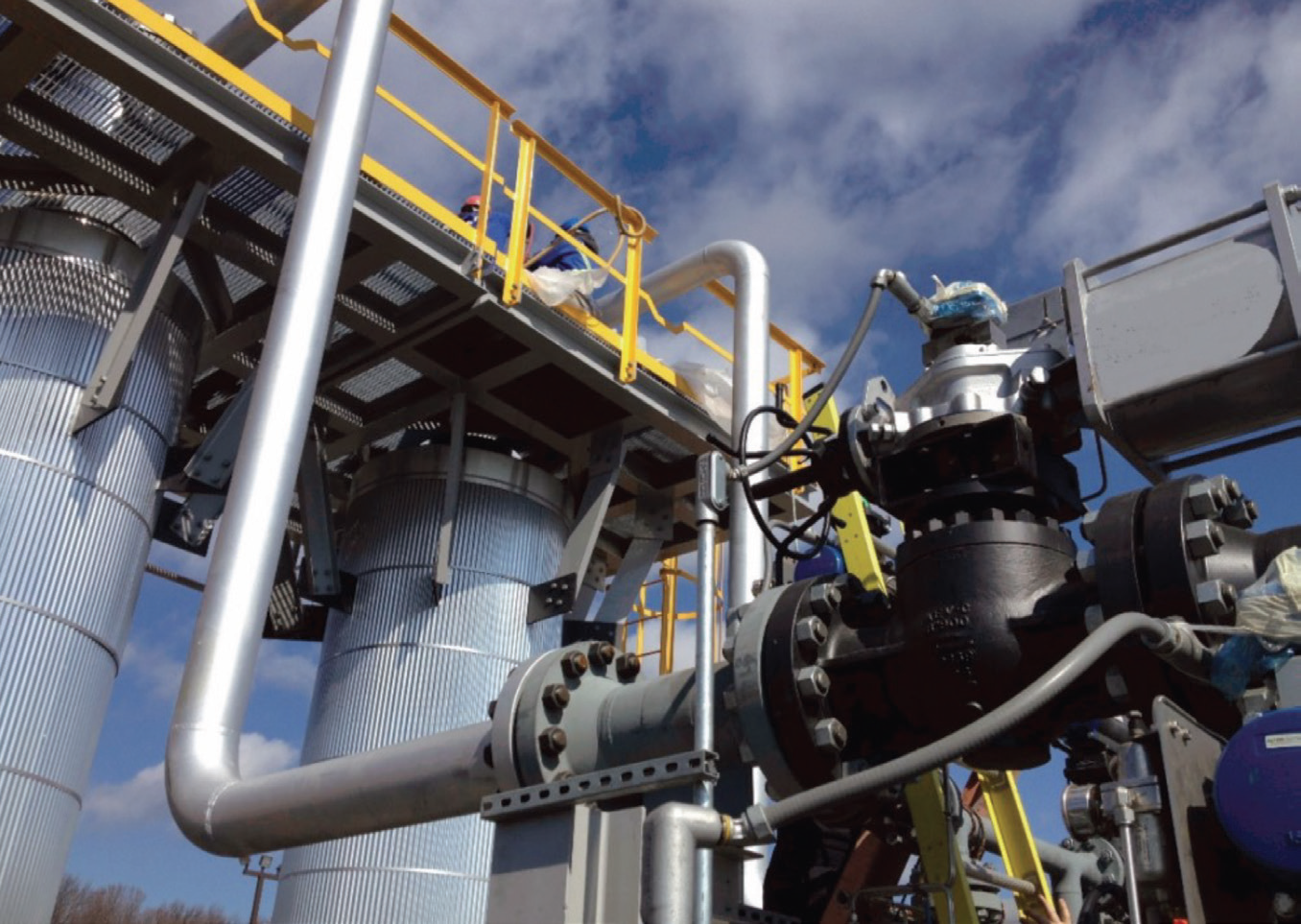
Valves with one or more of these application characteristics will often be a significant source of fugitive emissions. Rather than simply repairing the valve or installing a minor packing upgrade, end users should evaluate the current design and investigate the possibility of replacing it with a more suitable valve technology. While replacing the valve is expensive, the significant reduction in fugitive emissions, as well as higher performance and lower lifecycle maintenance costs, often justifies the expense.
An example of a process application with multiple fugitive emission risk factors are the switching valves used in molecular sieve service (Figure 5). The process requires tight sealing between the adsorption and regeneration streams, runs years between turnarounds, and cycles two to three times a day.
These service demands are difficult to meet, made more difficult by the constant thermal cycling and the presence of abrasive adsorbents in the process. Despite these conditions, the valves must continuously meet very strict fugitive emission requirements.
One company recently struggled mightily with the valves on their molecular sieve unit. They were performing yearly packing maintenance and rebuilding valves every three years, yet still struggled with repeated leak detection and repair violations and numerous fines. After struggling for years, the firm consulted with their valve vendor to determine if a different valve technology might ameliorate their issues.
After studying the problem, the client decided to replace the rising stem valves with torque seated quarter turn valves. The leak detection and repair violations immediately ceased, and the new valves required dramatically reduced maintenance, even as they performed better than the valves they replaced. Ultimately the valve upgrade project paid for itself in short order.
Conclusion
When facing fugitive emission challenges, end users should move beyond the typical response of increased monitoring and repair, and instead look carefully at the valve design. Often there are alternate designs that can resolve the emission problems and reduce operational costs.
It is best to start with the problem valves, seeking to replace the more troublesome equipment and upgrading as opportunities arise. Also, end users are wise to partner with knowledgeable valve vendors to take advantage of their expertise and learn the latest technologies available for each application. These vendors offer a wide range of options, and they can help evaluate various designs and verify the suitability of each for a particular application.
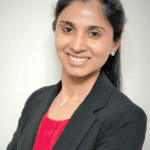