Technology is a gift. Advancements in technology have helped grow civilization faster than what many thought possible 100 years ago. Petroleum, chemical, and oil & gas industries have been users of tried-and-true methodologies, and for good reason. The switching costs associated with adopting new technology can be great when doing so requires the redesign of existing multi-billion-dollar infrastructure projects. However, our industry stands on the edge of significant technological advancements, and is about to experience a step change in production capabilities, profit preservation, and emissions reduction.
By Bronson Pate, Director of Global Fugitive Emissions, MagDrive Technologies
The valve design is overdue for a change. It can be best understood where the industry is heading in the future by reviewing where it has come from. Specifically, by looking at the history of valve design and the problems that advancements sought to solve.
Many say the first valve was developed during the Roman Empire and made of bronze. This valve consisted of a plug with a hole in it, a bottom support, and a dowel for turning the plug. Additional changes did not occur until the famous inventor Leonardo DaVinci developed several new designs in the 1400s. These lead to many advances in Renaissance – era valves. However, it was not until 1705, when the first steam engine was created, that new and improved valves were needed to regulate steam and high pressure.
As is the case with technological advancement, the need drove the change. Progress in one technology typically mandates progress in the technology that supports it. Lessons learned from steam engines also brought improvements to valves used in irrigation and plumbing. the door had been opened, and the 1800s and 1900s gave birth to valve manufacturing at scale.
Standardized Solutions
As the world’s energy needs increased, and moved from steam to fossil fuels, new problems arose shining a spotlight on fugitive emissions and leaking valves. The American Petroleum Institute (API) was established in 1919 and developed standards for valves to help reduce fugitive emissions in the U.S., specifically to the petroleum industry. A few years after API was established, the International Organization for Standardization (ISO) was founded in 1947 by 25 countries.
These two committees have developed the principal ‘Good Engineering Practices’ which are used most today. ISO 15848-1, API 622, 624, and 641 all have a significant impact on helping reduce the overall impact on the environment.
During the proposal of the regulations in the 1980s, the United States Environmental Protection Agency (USEPA) recognized ‘Leakless Equipment’. The proposed rules would not require leakless equipment, because it was not widely accepted, or the emission reduction per the control cost was unreasonable. Therefore, the USPEA allowed if someone wanted to use leakless equipment they would be allowed to as an alternative to compliance.
Some components per the USEPA can meet a definition of no detectable emissions (NDE). NDE is “indicated by an instrument reading of less than 500 ppm above background.”
The mid-2000s brought the first consent decrees requiring certified low leaking technology (CLLT) for all valves and packing newly installed into plant environments, limiting leaks to a <100 part per million by volume leak rate. These standards are applied to any new valve or packing in which is in volatile organic compound (VOC) gas vapor (GV) or light liquid (LL) service.
Valve standards like those listed are critical due to the fact that 90% of all fugitive emissions come from valves and connectors according to the USEPA stated in the “Leak Detection and Repair: A Best Practice Guide” of 2010. However, while all of the standards mentioned earlier help reduce fugitive emissions, reduction alone is not the goal. Each of these standards is chasing and pushing to the lowest possible limit, but no one has yet achieved the ultimate goal of zero leakage.

Chasing the Goal of Zero Emissions
In over 300+ reviews that I have conducted personally, I have only found afew sites that have installed NDE components. So, why are there not more of these components placed in facilities? Why is this such a challenge when the USPEA allows it, and based on the testing standards, proves the valves operate less than 100 ppm on average?
First, it could be that during the public comments of New Source Performance Standards VVa (NSPS VVa), USEPA stated,“no detectable emissions cannot be leaking at any point and are not under the same LDAR provisions as equipment not designated as such. If a piece of equipment designated as having no detectable emissions does leak, then it is not meeting the requirement in the rule.” With this statement it shows that the USEPA does not intend for NDE to be used unless the industry considers the component to truly be NDE as it would be an automatic violation if found leaking.
So, over many years no matter the testing, many components are still found to be leaking greater than 500 ppm. That point shows that no matter how many testing standards are in place, that valves still leak even when the best engineers in the world have designed a component to meet the most demanding standards. What if, within the industry, experts could genuinely find an NDE component or, better yet, only a component that never could have an indicated instrument reading more significant than the ambient air, or more commonly referred to as background?
Producing zero ppm components is a reality that has been around for many years on pumps. But within valves, it has shown significant improvement within the standards but has yet to reach a zero truly. What if technology has finally caught up on valves? Magnetic valves have been designed not only to meet NDE but also to meet a zero fugitive emission environment. Through magnetics, valves have finally been able to catch up to the world of zero fugitive emissions. To hit the global goal of net zero by 2050, these technological strides will be a strategic piece in achieving a viable net zero.
For the industry to keep pace, it must be agile and willing to seek change or advancement. This, in most scenarios, is quite understandable, as why change something when the ‘old’ way is still ‘working’ perfectly well? The problem is, it is not still working with current supporting technology and current understanding of environmental impacts. Many items come to light when talking about this type of change. For example, are magnets powerful enough to operate a valve? Magnetics have many great potential applications, but when used in valves, the strength that can be created is exceptionally outlandish.
A half-inch diameter shaft can be sheared when magnetic actuation creates 900 to 1000 in-lbs in torque. With this knowledge, one can calculate the infinite shear, allowing the magnets to skip when maximum torque has been achieved in either opening or closing. Do they work in high and low temperatures? They absolutely do. In fact, some magnets gain upwards of 40% additional strength at cryogenic temperatures. Even high temperatures, where leaks are often a major problem, some magnets can operate over 1000º F.
What is the working life of a magnetic valve? Since the valve is not relying on a dynamic packing with magnets, testing has showed a valve actuating over 40,000 additional actuations even after completing an API 6FA fire test. Does the footprint increase if magnetics are used? With some new technology, changes must be made to the existing structures.
The changes can be costly; in some cases, redesigning the existing infrastructure reduces technological advancement opportunities. With magnetics, the infrastructure does not have to be redesigned, and for a rising stem valve, you no longer have to worry about the stem sticking out and creating a hazard. As with any new technology, questions, and concerns are always at the forefront of any change.
Achieving Net Zero with Magnetic Actuation
Therefore, with some of the most challenging questions answered, the only possible question is: how can one truly have zero fugitive emissions? When exploring a traditional valve, at least 90% of all leaks can be found from the packing to the stem area, as both areas are dynamic. While there still may be a leak at the bonnet gasket in some cases, with it being a static seal, the ability for a leak to happen is extremely low. Magnetic actuators can be integrated into most standard valves as a retrofit. With this retrofit, the only potential leaking interface would be the gasket used when attaching to the bonnet.
All dynamic leaking interfaces have been removed, and the magnetic actuator is fully encapsulated with a solid wall and does not have any external actuation, thus making a magnetically actuated valve more like a check valve. The USEPA agrees, as published in the “Inspection Manual: Federal Equipment Leak Regulations for the Chemical Manufacturing Industry,” dated December 1998, that “Since a check valve has no stem or subsequent packing gland, it is not considered a potential source of fugitive emission and is not subject to the standards.”
So, two directions could be made when placing a magnetic Zero-E valve into service. The first could be to designate this component as NDE, which alllows the end user to only monitor the component once a year. Without having any external actuation, a Magnetic Zero-E control, gate, globe, plug, or ball valves could be classified categorically as check valves. Thus, removing all monitoring required for that component indefinitely.
If looking for ways to reduce emissions, Zero-E solutions will be a way of the future. Fugitive emissions have been listed as an ‘enforcement alert’ related to refineries since 1999. Since 2000, refineries have been under agreed settlements called consent decrees (CDs). These CDs have helped decrease emissions from refineries, but each facility hits a plateau in emission reduction. Zero-E solutions can interrupt these trends and begin to deliver emission reduction again. For example, if only 5% of leaking valves at a facility are exchanged for a Zero-E solution, a decrease of 63% in fugitive emissions can be reduced. The same reduction can be found if looking for a decline of CO2 for Net-Zero 2050 goals.
This reduction is not an estimate. Factors were achieved using actual reported emission data from valves at both facilities. In addition to delivering massive emission reduction, Zero-E solutions also eliminate the need to put a human into an operating facility for monitoring. Because, as discussed, Zero-E solutions like magnetic actuation eliminate the leak path entirely, monitoring requirements are either significantly reduced or nonexistent.
Considering the evolution and advancements in industry, processes have become more complex, experts have dug deeper, operate at more extreme temperatures and pressures, and are processing more harmful and lethal materials at a higher rate than ever before. With that, industry must consider the advancements in supporting technology. Collectively, there is also now understanding of the harsh impact of failure in these systems thanks to the advancements in monitoring and general environmental impact studies. What was potentially ‘working fine’ 50 years ago, may not be the best solution for today.
Albert Einstein said, “we cannot solve our problems with the same thinking we used when we created them”. Another way to look at is that the industry cannot solve the new problems with its old solutions. With the goal of net zero in industry, technologies like magnetically driven valves that truly provide a true Zero-Emission must be implemented.
Reference:
- https://www.epa.gov/sites/default/files/2014-02/ documents/ldarguide.pdf
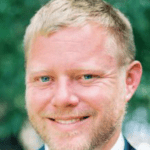