The health and safety of employees is of the utmost importance to industrial companies today; without the necessary engineers, technicians and maintenance operators keeping refineries operational, society as we know it would come to a swift halt. Oil is such a crucial component to our society – from clothing to ethanol-based hand sanitizers, to fueling cars, ships and jet planes. As oil and gas are essential, the industrial community is making valiant efforts to protect those on industry frontlines who are dedicated to keeping our energy flowing and cities running.
As a world-renowned manufacturer of infrared camera technologies for industry, FLIR Systems recently updated their products to incorporate key features sought after in the marketplace and prompted by the current global pandemic.
It is first important to understand the characteristics of ‘cooled vs uncooled’ optical gas imaging cameras, noting the specific wavelengths related to optical gas imaging and the detectors used within these cameras.
The two main wavelengths of OGI cameras are commonly referred to as midwave, 3-5 micrometer (μm), and longwave, 7-12 μm. In the gas imaging world, these may also be referred to as the ‘functional region’ and the ‘fingerprint region’, respectively. In the functional region, more gases from a single category can be seen by one camera, while many individual gases have specific absorption char-acteristics in the fingerprint region. For example, nearly all hydrocarbon gases absorb energy in the filtered region of the GF320 but have various absorption characteristics in the long-wave or fingerprint region. (1)
Cooled OGI cameras use detectors that require cooling to cryogen-ic temperatures and can be either midwave or longwave detectors. Midwave cameras can detect hydro-carbon gases such as methane and propane. Cooled longwave cameras are able to detect gases such as SF6. Cameras with cooled detectors have a filter that is attached to the detector that will prevent any stray radiation exchange between the filter and the detector, allowing for better image sensitivity. This increase in image sensitivity allows the visualization of certain gases that are applicable to regulatory standards.
Uncooled OGI cameras use a microbolometer detector that does not require the additional parts necessary to cool a detector. They are easier and less expensive to manufacture than cooled cameras but lack the sensitivity, or Noise Equivalent Temperature Difference (NETD), which makes it more difficult to visualize smaller gas leaks.
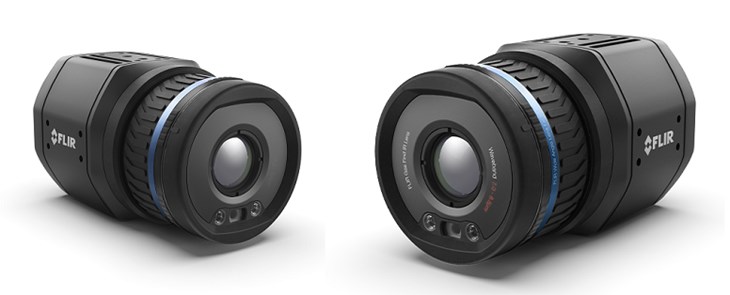
In response to recent COVID-19 developments, FLIR has adapted sever-al of its uncooled cameras for indus-try and elevated skin temperatures (EST) solutions. The FLIR A400/A700 Thermal Smart Sensor and Thermal Smart Image fixed camera for monitoring equipment are general, every-day automation cameras. The first, true thermo-graphic temperature automation camera was launched in the early 2000’s and revamped in 2007 with the release of the A320. “These new cameras hold the same ‘engine’ and detector as our other handheld temperature measurement cameras,” said Craig O’Neill, Director of Business Development at FLIR Systems. Why is that important? “If you can imagine, there are a lot of security cameras and visual cam-eras that sit and stare at things and only detect motion. In the oil and gas business, a lot of the faults and problems, especially as it relates to temperature, have nothing to do with motion, but instead with heat. Failures generally happen when a temperature level becomes higher.”
One application for these cameras is called critical vessel monitoring, where vessels inside refineries are covered in thermocouples. “If you think about a thermocouple it might get disbonded, or there may be 12-24 inches between each thermocouple; if this is truly a critical vessel, a lot of the times you may run into a scenario where it may be better to have a complete thermal image. Infrared camera can have hundreds of thousands of pixels in an image where each pixel is its own unique temperature measurement device. In this way, you will know that there is a temperature issue with said vessel and it needs to be diagnosed and attended to immediately,” said O’Neill.
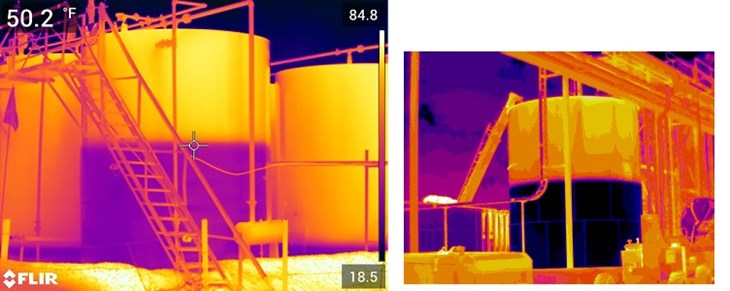
In 2020, the A400 and A700 cameras have pivoted to ensure that corporate offices, refineries and other related companies can monitor personnel entering the facility to ensure they do not have an elevated skin temperature, and potentially pose a community risk for COVID-19 transmission. “It actually measures the temperature of the tear duct of the eye. You can essentially set up one of these cameras and monitor every single person in the facility that passes by and quickly identify if someone has an elevated skin temperature.”
In addition to the need for a thermal camera to track and monitor employ-ees, as well as assets, the updates to the A400 and A700 were originally prompted by its late predecessor in 2007. “As you can imagine, what is important in an infrared camera is the sensor. In many cases, how well the sensor works and how well it can be integrated into your system is de pendent on the backend electronics.”
O’Neill reiterates the A400 and A700 has updated protocols that are necessary to be more easily integrated into modern systems in the market.
The recent GF77 allowed FLIR to broaden their scope of handheld products by assisting operators in being able to visually see methane. “This is not a broad hydrocarbon camera like our cooled systems. The GF77 will not meet EPA OOOOa or other regulatory standards, but it allows operators to see those large methane leaks, as the industry has heavily invested in methane reduc-tion technology in recent years. The GF77a is a fixed mount, continuously monitoring version of GF77, allowing automated detection of a gas leak onsite which can be displayed on a monitor.”
O’Neill mentioned two applications where this type of camera would be sought after. “Number one is safety. Customers are not solely concerned with small leaks that could be regulatory-compliance driven, but are concerned with their employees going into a potentially hazardous location with methane gas present – for example, on a well pad to ensure there are no leaks from a thief hatch or a valve on top of a tank. Operators will be able to monitor for those types of leaks from a safe distance,” said O’Neill. The second application he mentions is organizations participating in leak detection and repair (LDAR) programs for environmental stewardship reasons, outside of the regulatory compliance checkmark.
Join Craig O’Neill and the FLIR Systems team at Fugitive Emissions Summit Americas event, December 9-10, 2020 at Royal Sonesta Houston Galleria in Houston, Texas, USA.
1. O’Neill, C., & Lucier, R. (2019, February 28). Understanding Cooled vs Uncooled Optical Gas Imaging. Retrieved July 22, 2020, from https://www.flir. ca/discover/instruments/gas-detection/understanding-cooled-vs-uncooled-optical-gas-imaging/