By Cory Foytik, Principal, Comal Emissions Testing, LLC
Having performed hundreds of successful stack tests over 18 years in the industry, under the direction of dozens of Environmental Managers, the value added when a good test crew can deliver quality results in a timely fashion is apparent. Quality deliverables lead to lower stress levels and more time available for the EM’s other duties.
But how can one know when the test crew is following the QA/QC they are supposed to, and that there will be no surprises after agency review?
Recently, there was an audit by the Environmental Protection Agency (EPA) of 30 particulate matter (PM) stack test reports in Washington State. They identified errors in the application of test methods in over half of the 30 reports reviewed, and they found data missing in most of these reports. When these faulty stack tests are discovered there will be, at best, further time-consuming meetings and documentation required before being accepted and, at worst, a notice of violation sent, complete with a fine and requirement to redo the test. There are steps every EM can take to increase the chances of a drama-free test. Some of these are designed to help the test team while they are onsite at the client’s facility. Others are geared toward ensuring the testing company will deliver the quality results they are being paid for.

Quality Assurances
Unless the EM has experience with a specific stack testing company and project manager, the first step to maximizing the potential for a successful stack test is hiring a company that qualifies as an Air Emissions Testing Body (AETB). An AETB is a stack testing firm that meets the quality standards outlined in ASTM D-7036. AETB’s can either self-certify as such, or be accredited by a third party such as A2LA or STAC. The EM should first verify the vendor is an AETB by asking for a copy of their accreditation certificate (if accredited by a third-party) or their quality plan (if they are self-certified).
In fact, if the units being tested are electric generating units (EGUs) that supply power to the public energy grid and are regulated by Title 40 of the Code of Federal Regulations Part 75 (40CFR75), the testing must be performed by an AETB. This requirement does not extend to units covered by 40CFR60 or 40CFR63, but hiring an AETB is still the best first step to obtaining quality test results.
AETB’s are required to have onsite for all emissions measurements, including those for engineering purposes only, and at least one team member who is recognized as a Qualified Individual (QI). This means that for each method being performed there will be at least one individual onsite that has over a year of experience performing that method and has passed an exam that covers that method. The AETB should be able to forward the team member’s QI certification who will be leading the test effort to the EM in advance of the testing.
All AETB’s are also required to compose a test protocol for each stack test performed. These are required regardless of whether the tests are performed for engineering or compliance purposes. This helps to increase the amount of communication between the test crew and the client as well as the regulating body when it is a compliance test. When the testing is only performed for engineering purposes or is a relative accuracy test audit (RATA) it is not required to submit the protocol to the regulatory body, however, it is a good idea for the EM to request a copy of the protocol to ensure that it was first, completed as required and second, the scope of work in the protocol matches the expectations of the EM.
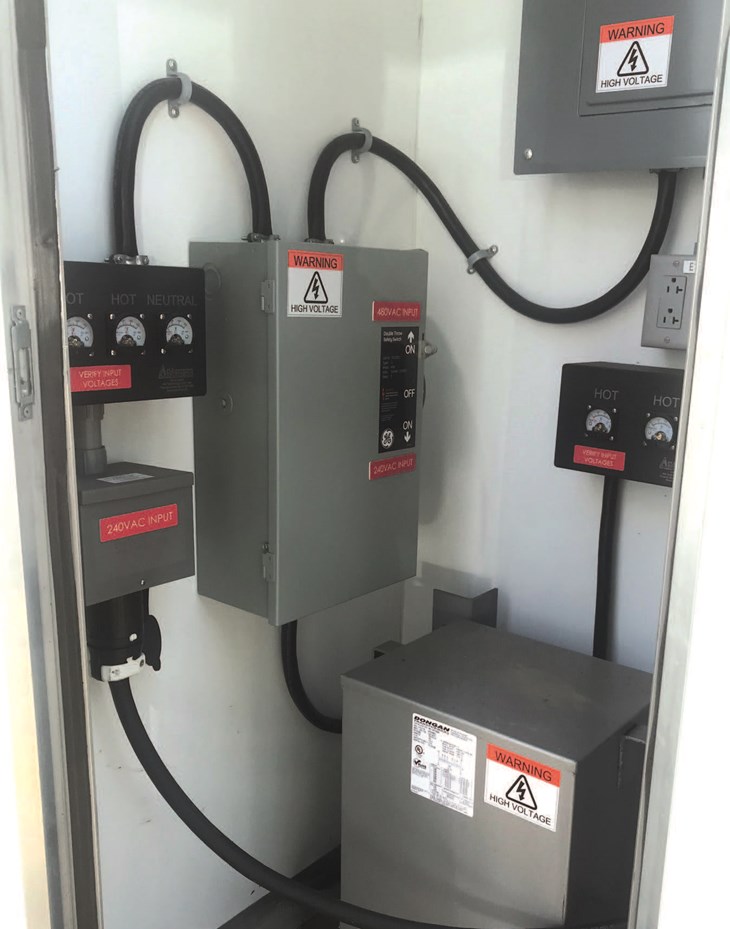
Site Preparation
Accessibility
Nearly every testing proposal ever written contains an assumption that the sampling ports on the unit to be tested will be clean, accessible, and obstruction free. This clause is beneficial to both the tester and client. There are not many things worse than setting up sampling equipment on a platform 200’ above ground level only to realize that the sampling port flanges have not been removed in years and the bolts either require a 36” pipe wrench or grinder to get off. Then once the flanges come off it is discovered that the ports are so packed with particulate matter a drill with a wire brush attachment is required to create access for the sampling probes. If the maintenance department is notified in advance of the testing that the ports should be inspected the week prior to the arrival of test team it can save hours or even an entire day of delay when the test team arrives onsite.
Additionally, the accessibility needs of the test team will vary depending on the analytes being measured. If the scope of work only includes concentration determination of pollutants that can be determined instrumentally (oxygen, carbon dioxide, sulfur dioxide, nitrogen oxides, carbon dioxide, and volatile organic compounds), it is possible only one port in the exhaust duct is needed and that port only needs to be one inch in diameter. If flow measurements are required to calculate mass emission rates, then a minimum of two ports are needed to perform a traverse across the duct, and those ports should be at least two inches in diameter. If the scope of work also includes determination of particulate matter, metal compounds, or other test methods that must be performed isokinetically, then the sample ports must be a minimum of four inches in diameter. The AETB project manager should communicate with the EM the needs of the test crew prior to mobilization, but if not, the EM can save themselves a lot of headaches during the testing by raising the topic in advance.
Power
Also usually found in the proposal’s list of assumptions is a power requirement. Typically, a test team performs their measurements out of an enclosed test trailer which will need power supplied to it either in the form of 120V, 240V, or 480V. Again, the AETB project manager should confirm with the EM prior to mobilization what type of power is needed and that it is available at site. If they do not and power is not available, this can lead to more unnecessary and costly delays.
Safety
Every EM knows that safety should be the number one priority on-site. The safety requirements of the site should be clearly conveyed to the test team prior to their arrival, particularly if the site requires training that lasts longer than 30 minutes or has drug-testing rules that require membership in NASAP or DISA.
In addition to a quality manual, every AETB also has an in-house safety manual. These can vary in content, but undoubtedly contain a requirement of the test team to perform and document a pre-job safety meeting with its crew. If your site requires a specific health and safety plan (HASP), that will satisfy this requirement. If you do not have site-specific requirements, ask to see the tester’s completed HASP. A test team that pays attention to safety requirements is more than likely a test team that pays attention to quality requirements.
Conclusion
By following the tips in this article, the EM will move the needle toward a stack test that results in quality data. However, this ultimately comes down to the performance of the test team and their project manager. When hiring a company or project manager that is unfamiliar, the best assurance may be to also hire a third party to oversee the testing. For a marginal increase in cost, third-party oversight can provide a massive increase in confidence of the results.
ABOUT THE AUTHOR
Cory Foytik is one of the founders and principals of Comal Emissions Testing, LLC. Cory has over 18 years of experience performing a wide range of stack tests for a for a large number of industrial clients. He has worked for multiple Air Emissions Testing Bodies throughout his career and most recently held the title of Regional Vice President at his previous employer. Currently he is focused on building a business that provides high-quality results for both end users and AETB partners.