The term ‘emissions’ has become a buzzword for many social and political discussions revolving around pollution and the impact of industrialization on climate change. Fugitive emissions can be categorized as uncontrolled, nonintentional leaks and other irregular releases of gases or vapors from a pressurized containment system, such as appliances, storage tanks, pipelines, wells, or other pieces of equipment, and are typically produced through industrial activities. The International Organization of Oil and Gas Producers has worked independently and with many third-party organizations to come up with several technologies to help detect, locate, and remedy these emissions.
By Foster Voelker II and Mike Dunn
Emissions Detection Technologies
Fugitive emissions research and development refers to the study and improvement of methods to detect, measure, and reduce emissions. Currently utilized infrared methods include gas chromatography-mass spectrometry (GC-MS) and fourier-transform infrared spectroscopy (FTIR).
Gas chromatography-mass spectrometry (GC-MS) can be used to track down invisible contaminants. This technology is employed in a targeted area to detect and identify fugitive emissions in the atmosphere by investigating the emissions’ causes, pathways, and mitigation options.
Fugitive emission detection using infrared technology can also be accomplished using fourier-transform infrared spectroscopy (FTIR). FTIR1 obtains an infrared spectrum of absorption or emission of a solid, liquid, or gas, and identifies the presence of organic and inorganic compounds in the sample. Depending on the infrared absorption frequency range, the specific molecular groups prevailing in the sample will be determined through spectrum data in the automated software of spectroscopy.
Other, less widely used methods to control fugitive emissions include:
- Detecting leaks by monitoring temperature increase caused by gas escape.
- Utilizing gas chromatography, which identifies the composition and concentration of exhaust gas.
- Utilizing mass spectrometry to identify the type and amount of gas escaping through a leak.
- Training dogs to employ their acute sense of smell to detect the presence of gases like methane.
- Acoustic emission detection, in which sensors listen for the sound of a gas leak and pinpoint its location.
- Optical Emission Spectroscopy, which uses sensors to track the light from the escaping gas.
Why Use Infrared technologies?
Oil & gas production, refining, and processing facilities are among those that have used infrared (IR) technology to search for and monitor fugitive emissions. GC-MS and FTIR can be used together to track the levels of fugitive emissions in the air and assess how they affect air quality.
The benefit of IR technology is that it can monitor fugitive emissions in real time and in continuous detail. The information it gathers can be used to better understand and control industrial processes and locate and quantify potential emission sources. Infrared technologies can also create a source-specific emission profile, which helps identify and characterize emission sources.
In addition to oil & gas production, refining, and processing facilities, IR technology can be used to monitor emissions in many other industrial operations. Data gathered can be utilized for process optimization and management, as well as to identify and measure possible emission sources. Source-specific emission profiles can be created, which can be helpful for research into the characterization of emission sources.6
Using IR and IOGP together
A more precise picture of a plant’s emissions can be obtained by combining infrared (IR) technology and infrared optical gas pyrometry (IOGP). According to Omega.com, an infrared pyrometer, also known as a radiation thermometer, is any non-contacting device intercepting and measuring thermal radiation emitted from an object to determine surface temperature. The data these two techniques collect can be utilized for process optimization and management, as well as to identify and measure possible emission sources or verify the results of previous emission investigations.
Caveats to Using IR or IOGP Technology
There are several potential problems with employing IR or IOGP technology to identify fugitive emissions. The first is the possibility of a false positive, in which an emissions signal is picked up, but there is no actual emission. False positives may arise for several reasons. The environment, nearby objects reflecting light, or various other factors could be to blame. The accuracy of a reading can also be affected by the speed and direction of the wind, making it hard to precisely quantify emissions from a particular source. Furthermore, interference from other infrared radiation sources, such as the sun or other industrial sources, may make it difficult to detect and identify an emission source. Infrared light is sensitive to many things in the atmosphere, thus accurate calibration of the spectrometer is essential.
Looking Forward
Technologies using IR spectronomy and IOGP to detect fugitive emissions have a bright future; further study and development should lead to better air quality and fewer greenhouse gas emissions.3 It is essential that innovators in these industries continue to collaborate to create industry-wide best practices for controlling fugitive emissions.
Future initiatives within the industry include:
- Developing more precise methods of detecting and monitoring fugitive emissions.
- Improving repair and maintenance practices to prevent and lower fugitive emissions.
- Collaborating with the EPA, LDAR (Leak Detection and Repair) organizations, Fugitive Emissions Consultants and other regulators and authorities to reduce fugitive emissions.
- Encouraging businesses to voluntarily report results of fugitive emissions testing.
- Conducting state-of-the-art research on state-of-the-art technologies to control fugitive emissions.
Oil & gas producers have already spent billions of dollars researching and developing systems to help reduce fugitive emissions. Some solutions generated from this research include improving leak detection and repair, installing vapor-recovery units, applying state-of-the art seals, electrifying equipment (for example, replacing gas boilers with electric steam production systems), and reducing routine and non-routine flaring by introducing predictive maintenance and improving and expanding gas processing. For downstream operations, energy efficiency improvements and rotating equipment electrification could be a major lever, alongside switching to zero-emissions hydrogen (green or blue), renewable power and heat sources (such as solar photovoltaic (PV), biomass and biomethane), or carbon capture utilization and storage. Switching to bio-based or circular feedstocks could also help reduce the Scope 3 footprint. Many of these levers save money and can pay back the required investment within a few years.5
Conclusion
Before deciding the proper strategy to implement, several factors must be considered. The nature of the gas emitted is the most crucial aspect, since different gases call for distinctive mitigation approaches. The cost and convenience of executing the reduction technique should also be considered.
IR and IOGP each have benefits and drawbacks regarding lowering fugitive emissions. IR is more flexible and more accurate, although it comes with a steeper upfront cost. IOGP is less costly to implement, and it is simpler to produce readings, however it cannot be automated and so must be done manually. The best strategy to reduce fugitive emissions, then, is to combine IR with IOGP, thereby achieving reduced emissions while holding costs to a minimum.10
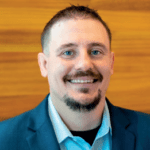

References
- https://en.wikipedia.org/wiki/Fourier-transform_infrared_spectroscopy, n.d.
- https://en.wikipedia.org/wiki/Fugitive_emission, n.d.
- Abraham-Dukuma, M. C. (2021). The role of law in climate change mitigation in oil and gas production. (Doctoral dissertation, The University of Waikato).
- Bell, C. S., Vaughn, T., & Zimmerle, D. (2020). Evaluation of next generation emission measurement technologies under repeatable test protocols. Elementa: Science of the Anthropocene, 8.
- Bouchene, L., Cassim, Z., Engel, H., Jayaram, K., & Kendall, A. (2021, December 13). Green Africa: A growth and resilience agenda for the continent. McKinsey & Company. Retrieved November 21, 2022, from https://www.mckinsey. com/capabilities/sustainability/our-insights/green-africa-a-growth-and-resilience-agenda-for-the-continent
- Poot, B., Tegami, A., Brown, W., Convery, A., Stranden, T. K., Bryant, E., … & Hardeveld, W. (2020, July). Our Industry’s Journey in Measuring Methane Emissions and Where We’re Going from Here. SPE International Conference and Exhibition on Health, Safety, Environment, and Sustainability. OnePetro.
- P. Mohamed Shameer, P. Mohamed Nishath, in Advanced Biofuels, 2019.
- Okparanma, R. N., Araka, P. P., Ayotamuno, J. M., & Mouazen, A. M. (2018). Towards enhancing sustainable reuse of pre-treated drill cuttings for construction purposes by near-infrared analysis: A review. Journal of Civil Engineering and Construction Technology, 9(3), 19-39.
- Riley, D., Schaafsma, M., Marin-Moreno, H., & Minshull, T. A. (2020). A social, environmental and economic evaluation protocol for potential gas hydrate exploitation projects. Applied Energy, 263, 114651.
- Reuben, N. O., Perez, P. A., Josiah, M. A., & Abdul, M. M. (2018). Towards enhancing sustainable reuse of pre-treated drill cuttings for construction purposes by near-infrared analysis: A review. Journal of Civil Engineering and Construction Technology, 9(3), 19-39.